Table of Contents
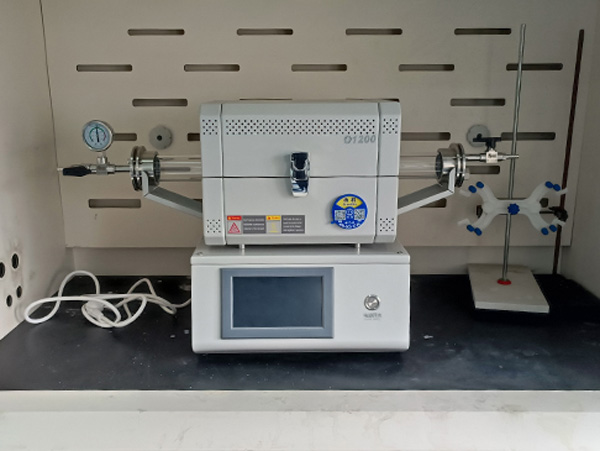
What is a Tube Furnace?
Introduction
A tube furnace is a type of high-temperature electric furnace commonly used in laboratories and industries, primarily for various applications such as material synthesis, heat treatment, and atmosphere control experiments.
Its basic structure includes a heating element, a hollow tubular chamber (usually made of quartz or ceramic), and a temperature control system.
The tube furnace generates a high-temperature environment inside the tube for heating treatment.
Main Structure
Furnace Tube
The core component of a tube furnace is a tubular chamber, usually made of high-temperature-resistant materials such as quartz or alumina, which can maintain chemical stability at high temperatures. Samples are typically placed inside the tube, and specific experiments are conducted through external atmosphere control.
Click to view ” What is the Tube Furnace Tube Made Of? An In-Depth Analysis “
Heating Element
The heating element is arranged outside the furnace tube, usually made of materials such as resistance wire or silicon carbide rods, capable of providing high temperatures ranging from 1200°C to 1700°C.
Temperature Control System
The tube furnace employs an intelligent PID fuzzy temperature control system, featuring a 7-inch true color touchscreen input, real-time heating power display, nonlinear temperature correction, and functions such as over-temperature alarm, disconnection warning, and leakage protection.
Types
Classified by Heating Zones
Single-Zone Tube Furnace
This type has only one heating zone, ensuring uniform temperature across the heating area of the entire tube. It is suitable for experiments that require a constant temperature, commonly used in simple material heat treatment experiments.
Multi-Zone Tube Furnace
This type features multiple independent heating zones, allowing the temperature of each zone to be controlled separately, creating different temperature gradients. It is ideal for experiments that require multiple temperature settings or thermal analysis, such as gradient temperature descent or complex reaction processes.
Classified by Key Usage
Atmospheric Pressure Tube Furnace
Heating experiments are conducted under atmospheric pressure, with the internal pressure of the tube consistent with the external air pressure. Suitable for general material heat treatments and routine experiments.
Vacuum Tube Furnace
By using vacuum equipment to remove air from the tube, heating is conducted in a vacuum environment. This is ideal for experiments involving air-sensitive materials, preventing the sample from reacting with oxygen. Applications include processes like metal reduction, material synthesis, or vapor deposition.
Atmosphere Furnace
This type allows the introduction of inert gases (such as nitrogen or argon) or reducing gases (such as hydrogen) through an inlet to maintain a controlled atmosphere. It is suitable for experiments requiring a specific atmosphere, such as gas-solid reactions, chemical vapor deposition (CVD), or special material processing.
Click to view ” What is the Use of Hydrogen in the Tube Furnace? “
Classified by Operation Mode
Horizontal Tube Furnace
The tube is placed horizontally, commonly used in routine experiments, suitable for batch processing of samples or experiments that require uniform heating.
Vertical Tube Furnace
The tube is placed vertically, suitable for experiments where samples are vertically loaded after placement, particularly for experiments that involve sedimentation or fluid reactions. It is commonly used in gas-solid reactions, liquid vaporization, chemical reaction experiments, etc.
Rotary Tube Furnace
The tube can rotate, suitable for experiments that require uniform stirring or mixing of samples. The rotation ensures that solid samples are evenly distributed during the heating process.
Click to view” Rotary Tube Furnace Price: Factors, Trends, and ZYLAB’s Advantage. “
Classified by Operating Temperature
Low-Temperature Tube Furnace
The operating temperature range is typically between 400°C and 800°C, suitable for low-temperature material processing, such as polymer pyrolysis and catalytic reactions.
Medium-Temperature Tube Furnace
The operating temperature range is between 800°C and 1200°C, suitable for the heat treatment of most materials, such as ceramic sintering, metal annealing, and material heat treatment.
High-Temperature Tube Furnace
The operating temperature range is between 1200°C and 1700°C, suitable for high-temperature material synthesis, vapor deposition, and high-temperature metal combustion experiments.
Click to view ” Understanding Tube Furnace Temperatures: Medium vs. High-Temperature Applications. “
Features
- Humanized design, stable and durable quality.
- 30-segment programmable automatic control.
- Intelligent 7-inch color touch screen, making operation more intuitive and convenient.
- Allows presetting of 15 sintering curves, avoiding the hassle of repeated settings for different experimental processes.
- Double-layer steel shell with fan cooling, ensuring the furnace surface temperature stays below 50°C.
Applications of Tube Furnace
Material Science and Research
Material Sintering: Tube furnaces are widely used in the sintering process of ceramics, metals, and composite materials. At high temperatures, material particles densify through diffusion, rearrangement, and grain growth to form high-performance materials.
Powder Metallurgy: Tube furnaces heat metal or alloy powders to sinter them into shape at high temperatures. This method is used to manufacture precision metal parts or composites, applicable in aerospace, automotive, electronics, and other industries.
Nanomaterial Preparation: Tube furnaces are used to produce nanomaterials like carbon nanotubes and graphene. Under a high-temperature atmosphere, reactants generate nanomaterials with uniform structure and excellent properties, used in energy storage, electronic devices, and sensors.
Chemical Reactions and Synthesis
Chemical Vapor Deposition (CVD): In CVD processes, tube furnaces heat reactive gases to deposit thin films or coatings on substrates. CVD technology is widely used in semiconductor device manufacturing, optical films, and wear-resistant coatings.
Catalytic Reaction Research: Tube furnaces are suitable for gas-solid reactions, commonly used for catalyst synthesis, testing, and studying catalytic reaction mechanisms. They simulate industrial conditions to explore the kinetics and mechanisms of chemical catalytic reactions.
Pyrolysis and Reduction Reactions: Tube furnaces are used in pyrolysis processes to heat organic or inorganic substances, breaking them down into gaseous or solid products. In reduction reactions, tube furnaces reduce metal oxides to metals at high temperatures, often for metal extraction or metallurgical processes.
Semiconductor Industry
Diffusion and Annealing Processes: Tube furnaces are used for diffusion and annealing in semiconductor materials. Diffusion introduces dopants into silicon wafers to alter their electrical properties, while annealing eliminates crystal defects and improves material quality.
Thin Film Growth: Tube furnaces are employed in epitaxial growth and thin film deposition processes. Under high temperatures, atoms or molecules deposit on a wafer surface to form high-quality thin-film structures, used in transistors, optoelectronic devices, and other semiconductor components.
Environmental Science and Energy Research
Carbon Capture and Storage (CCS): In CCS research, tube furnaces are used to study the absorption, decomposition, or transformation of carbon dioxide under high-temperature conditions, aiding the development of new technologies to reduce greenhouse gas emissions.
Biomass Conversion and Pyrolysis: Tube furnaces are used for the pyrolysis and gasification of biomass. Under high-temperature conditions, biomass decomposes into combustible gases and biochar, with the research results contributing to renewable energy development and environmental protection.
Metallurgy and Metal Processing
Metal Heat Treatment: Tube furnaces are used for annealing, quenching, and tempering metal materials, adjusting their microstructure and mechanical properties. These processes are widely used in manufacturing, particularly in the production of tools and mechanical parts.
High-Temperature Alloy Research: Tube furnaces treat metal alloys under high-temperature atmospheres to produce high-temperature, corrosion-resistant alloy materials. These materials are often used in aerospace, nuclear energy, and other industries that demand extreme material performance.
Geology and Mineralogy
Rock Melting and Mineral Analysis: In geological research, tube furnaces are used for rock melting experiments to simulate magma activity under high-temperature conditions, studying mineral formation and melting behavior.
Mineral Heat Treatment: Tube furnaces heat minerals or ores to study their physical and chemical properties, commonly used in mineral resource development, mineral separation, and purification processes.
High-Temperature Material Synthesis
Refractory Material Preparation: Tube furnaces produce high-temperature ceramic or composite materials, widely used in high-temperature equipment in metallurgy, energy, and chemical industries.
Oxide Material Preparation: Tube furnaces synthesize oxide materials, such as alumina and zirconia, under high temperatures. These materials are commonly used in catalysts, coatings, and electronic ceramics.
Pharmaceutical and Biotechnology
Biomaterial Heat Treatment: Tube furnaces prepare biomaterials, conducting heat treatment and thermal degradation experiments to study the stability and degradation behavior of materials under high temperatures, applied in drug preparation and medical device development.
Compound Thermal Decomposition: In pharmaceutical research, tube furnaces are used for the thermal decomposition of drug intermediates or compounds, studying their thermal stability and decomposition products.
New Energy and Battery Research
Lithium Battery Material Preparation: Tube furnaces are used for high-temperature treatment of lithium battery cathode and anode materials, such as lithium iron phosphate and nickel-cobalt-manganese oxides, to improve their electrochemical properties. High-temperature sintering enhances the conductivity and structural stability of materials.
Fuel Cell Research: In fuel cell research, tube furnaces are used to prepare and test electrode and electrolyte materials, such as ceramic materials in solid oxide fuel cells (SOFCs).
Teaching and Laboratory Research
Education and Basic Experiments: Tube furnaces are commonly used in basic experiments in universities and research institutions in disciplines such as materials science, physical chemistry, and environmental engineering. Students learn and master high-temperature processing techniques through experimentation with tube furnaces.
Laboratory Research and Development: In R&D labs, tube furnaces are used for small-scale material synthesis, catalytic research, and process development, helping scientists explore new materials and processes.
Why Use ZYLAB Tube Furnace?
Precise Temperature Control
Equipped with an advanced PID self-learning fuzzy control system, tube furnaces can achieve accurate temperature control, maintaining within ±1°C. This is crucial for temperature stability and reproducibility during experiments.
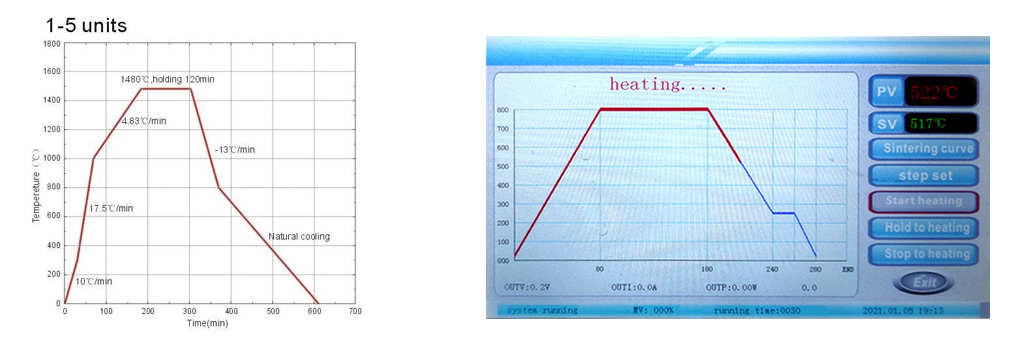
It allows for up to 30 independent temperature control stages and 15 preset sintering curves, enabling materials to be processed or chemical reactions to proceed as expected under specific conditions.
Uniform Heating
The heating elements are arranged around the tube, ensuring the sample receives uniform thermal radiation throughout the entire tube.
High-Temperature Capability
The furnace chamber is vacuum-formed and made from high-purity alumina refractory materials, allowing the tube furnace to reach extremely high temperatures, typically between 1200°C and 1700°C, or even higher.
Multiple Atmosphere Control
Tube furnaces can conduct experiments under various atmospheres, such as air, inert gases, vacuum, or reducing atmospheres. Equipped with gas flow meters, atmosphere sintering becomes more convenient.
For experiments involving gas-solid reactions or those that require avoiding oxidation, atmosphere control is crucial. For instance, in semiconductor manufacturing or catalyst synthesis, specific inert or reducing atmospheres are needed to ensure experimental success.
Material Versatility
The furnace tube can be made from various materials, such as quartz or alumina, allowing for the selection of the appropriate tube material based on experimental needs, ensuring no adverse reactions between the sample and the furnace tube.
Ease of Operation
Laboratory tube furnaces are compact and space-efficient, making them ideal for laboratory environments. The separation of heating elements from the furnace tube ensures easy sample handling, especially when frequent sample changes are required.
Energy Efficiency
Using specialized furnace linings and high-quality silicon carbide heating elements, tube furnaces heat up quickly and maintain temperature, reducing energy consumption. Many tube furnaces also integrate heat recovery systems, further reducing energy usage.
How to Properly Use a Tube Furnace?
Basic Steps
1. Preparatory Work
Equipment Check:
Inspect the tube furnace’s power cord, gas lines, and vacuum system to ensure they are functioning properly.
Ensure the furnace tube and insulation plugs are undamaged, and clean the inside of the furnace tube.
Sample Preparation:
Place the sample to be processed in the center of the furnace tube, making sure it does not touch the tube walls.
Use an appropriate sample boat and position it in the middle of the furnace chamber.
2. Installation and Connection
Install the Furnace Tube:
Symmetrically place the furnace tube in the center of the furnace chamber and secure it with flanges and screws, ensuring the flanges are properly aligned.
Gas Line Connection:
Open the gas line following the sequence of the main valve on the gas cylinder, the pressure-reducing valve, and the pipeline switch.
Confirm the appropriate gas flow; typically, one continuous bubble in the safety bottle is the standard.
3. Setup and Start
Set Temperature Curve:
Design the heating and cooling curves based on the experimental requirements, setting the heating and cooling rates.
Ensure the set furnace temperature meets the requirements for sample sintering or heat treatment.
Pre-start Check:
Ensure all valves are closed, and the gas flow is normal.
Confirm that all instruments and equipment are in their initial state.
Start Heating:
Turn on the power, enter the program temperature settings, and press the heating button to start the process.
Monitor temperature changes to ensure it follows the set curve.
4. Monitoring and Adjustment
Real-time Monitoring:
During heating and cooling, continuously monitor the furnace’s internal pressure, temperature, and gas flow.
Watch for bubbles at the exhaust end to ensure there is no blockage.
Handling Abnormal Situations:
If bubbles disappear or pressure abnormalities are observed, immediately stop the furnace for inspection.
In case of gas supply depletion or equipment failure, promptly replace the gas source or contact technical support.
5. Ending Operation
Natural Cooling:
After the procedure is complete, allow the furnace to naturally cool to below 100°C before stopping the gas flow.
Do not forcibly open the furnace chamber to avoid safety risks.
Equipment Cleaning:
After removing the sample, clean the inside of the furnace tube and surrounding area to ensure the equipment is tidy.
Once the equipment has completely cooled, turn off the gas cylinder and power.
Precautions
1. Preheating Before First Use or After Extended Downtime
When using the furnace for the first time or after a long period of inactivity, preheating is necessary. The furnace should be baked at around 120°C for 1 hour, and then at around 300°C for 2 hours to prevent cracking of the furnace chamber.
During use, the furnace temperature should not exceed the rated temperature to avoid damaging the heating elements and furnace lining.
It is prohibited to pour liquids or molten metals directly into the furnace chamber. Keep the inside of the chamber clean.
2. Quartz Tube Usage Precautions
When using a quartz tube in the tube furnace at temperatures above 1000°C, the high-temperature part of the quartz tube may become opaque. This phenomenon, known as “devitrification,” is an inherent characteristic of quartz tubes and is normal, so there is no need for concern.
3. Temperature Ramp Rate Control
In a cold furnace, the chamber absorbs a large amount of heat, so the temperature ramp rate in the low-temperature range should not be too fast. There should also not be significant differences in ramp rates across different temperature ranges.
When setting the temperature ramp rate, it should be adjusted reasonably according to the physical and chemical properties of the sintered material to prevent material spillage, which could contaminate the furnace tube.
4. Regular Inspection of the Electrical System
Regularly check the contact quality of electrical connections in the temperature control system, especially at the connection points of the heating elements. Ensure they are securely connected to avoid malfunction due to poor contact.
ZYLAB Tube Furnaces
ZYLAB Tube Furnaces offer precise temperature control, excellent thermal uniformity, and versatility in applications such as annealing, sintering, heat treatment, and chemical reactions. They are ideal for processes that require a controlled atmosphere or specific heating profiles, making them indispensable tools in materials science, chemistry, and other scientific disciplines.
ZYLAB provides a comprehensive selection of furnaces specifically designed for tube-based applications. Here, you will find information on various models, sizes, and temperature ranges available, along with their unique features and capabilities. Whether you need a single-zone or multi-zone furnace, horizontal or vertical configuration, we offer a range of options to suit your specific requirements.
ZYLAB experts team always ready to help you find possible solutions for optimum performance. If you have a requirement, contact us now!