Table of Contents
Overview
A tube furnace is a type of high-temperature heating device used in various laboratory and industrial applications. It consists of a cylindrical chamber (tube) made of refractory material, often quartz or ceramic, which can withstand high temperatures without undergoing deformation.
The furnace is designed to heat materials to elevated temperatures in a controlled environment.
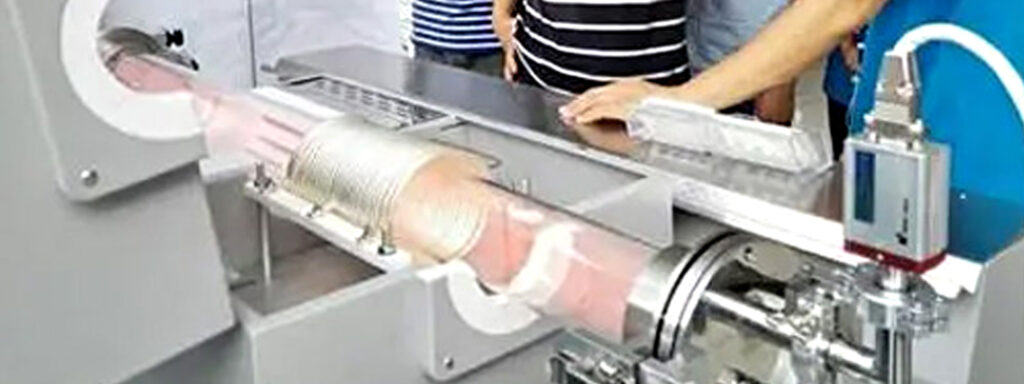
Features
Construction: The main component of a tube furnace is the heating chamber or tube, which is usually long and cylindrical in shape. The tube is enclosed within a larger outer casing made of metal to provide thermal insulation and safety.
Heating elements: Inside the tube, there are one or more heating elements, made of high-temperature resistance wire or molybdenum disilicide or silicon carbide, that generate the heat when an electric current passes through them. The number and placement of the heating elements can vary depending on the specific design of the furnace.
Temperature control: Tube furnaces are equipped with a temperature control system that regulates the amount of current flowing through the heating elements to achieve and maintain the desired temperature and allow precise temperature settings and adjustments.
Sample placement: The material to be heated (sample) is placed inside the tube on a sample holder or a boat made of a refractory material that can withstand high temperatures. The sample is typically positioned in the center of the tube to ensure uniform heating.
Gas atmosphere: In some applications, tube furnaces can be operated with a controlled gas atmosphere, such as nitrogen, argon. This allows researchers to perform heat treatments under specific environmental condition
Work Process
Sample Preparation: The sample should be prepared in the form of a tube or a crucible that can fit into the tube furnace.
Loading Sample: The sample is loaded into the tube furnace, and the tube furnace is closed.
Setting Temperature: The desired temperature is set using the temperature controller.
Heating: The tube furnace heats the sample to the desired temperature at a controlled heating rate.
Cooling: The tube furnace is allowed to cool down to the ambient temperature.
Applications
Tube furnaces have a wide range of applications in both laboratory and industrial settings. Some of the key applications include:
Materials Research: Tube furnaces are extensively used in materials research to study the behavior of various materials at high temperatures. Researchers can investigate phase transitions, crystal growth, and thermal properties of materials.
Sample Preparation: In laboratories, tube furnaces are commonly used for sample preparation techniques, such as annealing, calcination, and sintering. These processes are crucial for preparing samples with specific properties for further analysis.
Heat Treatment of Metals and Alloys: Tube furnaces are employed in industries for heat treatment processes like annealing, tempering, quenching, and hardening of metals and alloys. These treatments improve the mechanical properties and remove internal stresses in materials.
Catalysis Research: Catalysis studies often involve high-temperature reactions. Tube furnaces provide a controlled environment for investigating catalytic processes and developing more efficient catalysts.
Synthesis of Nanomaterials: Tube furnaces play a vital role in the synthesis of nanomaterials. By precisely controlling temperature and gas atmospheres, researchers can produce nanoparticles, nanotubes, and other nanostructures with desired properties.
Thermal Analysis: Tube furnaces are used in thermal analysis techniques like thermogravimetric analysis (TGA) and differential scanning calorimetry (DSC). These methods help determine the thermal stability and behavior of materials.
Powder Metallurgy: In powder metallurgy processes, tube furnaces are used to sinter metal powders into solid components with controlled porosity and density.
Glass and Ceramic Production: Tube furnaces are used in glass and ceramic industries for melting, annealing, and shaping processes.
Environmental Simulation: Some tube furnaces are designed to simulate specific environmental conditions, such as high-temperature and controlled atmosphere testing for aerospace and materials engineering applications.
Research and Development: Tube furnaces are valuable tools in various research and development activities across different scientific disciplines. They enable scientists and engineers to explore high-temperature processes and develop new materials and technologies.
It’s important to note that the specific applications of tube furnaces may vary based on their design, temperature range, and additional features, such as gas flow control and vacuum capabilities.
Additionally, the versatility and reliability of tube furnaces make them indispensable in a wide range of scientific and industrial pursuits.
Benefits
Tube furnaces offer several benefits that make them valuable tools in laboratory and industrial settings. Some of the key benefits include:
High-Temperature Capability: Tube furnaces are designed to achieve and maintain high temperatures, often exceeding 1000°C (1832°F) or even higher upto 1700.C. This capability allows researchers and industries to perform processes that require extreme heat, such as materials synthesis, heat treatment, and thermal analysis.
Uniform Heating: Tube furnaces provide uniform heating along the length of the tube, ensuring consistent and predictable temperature profiles within the heating zone. This uniformity is crucial for accurate and reproducible results in experiments and industrial processes.
Controlled Atmosphere: Many tube furnaces can operate in controlled gas atmospheres, such as nitrogen, argon. This feature enables researchers to perform heat treatments and chemical reactions in specific environments, simulating real-world conditions and studying the effects of different gases on materials.
Versatility: Tube furnaces are versatile tools that can accommodate a wide range of sample sizes and shapes. They can handle various materials, from solids to powders and thin films, making them suitable for diverse applications.
Precise Temperature Control: Many tube furnaces come equipped with intelligent temperature controllers, allowing users to set and maintain precise temperature levels. This level of control is essential for accurately reproducing experimental conditions and achieving specific material properties.
Fast Heating and Cooling Rates: Tube furnaces can reach high temperatures relatively quickly, and their efficient insulation allows for rapid cooling rates. This feature is beneficial for time-sensitive experiments and processes.
Easy Maintenance: Tube furnaces are generally straightforward to maintain, with removable and replaceable heating elements and insulation. Regular maintenance ensures their longevity and reliable performance over time.
Safety: Tube furnaces are designed with safety features to prevent accidents, such as overheat protection and safety interlocks. Additionally, the outer casing stays relatively cool during operation, reducing the risk of accidental burns.
Energy Efficiency: Many modern tube furnaces are designed with energy-efficient features to minimize power consumption while maintaining high-temperature performance.
Compact Size: Tube furnaces are often compact and occupy relatively small laboratory or workspace footprints. Their small size allows for easy integration into existing setups and laboratory environments.
Scale-Up Possibility: In industrial applications, tube furnaces can be scaled up to accommodate larger quantities of materials while maintaining similar heating characteristics.
Overall, tube furnaces are indispensable tools for high-temperature research, materials processing, and a wide range of industrial applications.
Their combination of high-temperature capabilities, precise control, and safety features make them essential for advancing scientific knowledge and technological advancements in various fields.
Price
The price of a tube furnace can vary significantly depending on several factors, including the brand, specifications, temperature range, size, and additional features.
Generally, high-quality tube furnaces with advanced temperature control and safety features will be more expensive than basic models.
Basic laboratory-grade tube furnaces with temperature ranges up to 1200°C could start at around $1,500 to $5,000 USD.
However, more advanced models with higher temperature capabilities (e.g., 1500°C to 1700°C) or larger sizes could range from $5,000 to $20,000 USD or more.
Different suppliers and distributors may offer varying prices for tube furnaces.
To get accurate and up-to-date pricing information, it is best to contact reputable suppliers directly and request a quote based on your specific requirements.
Considerations When Purchasing
When purchasing a tube furnace, several important factors should be considered to ensure that you select the right model that meets your specific needs and requirements. Here are some key considerations:
Temperature Range: Determine the maximum temperature you need for your intended applications. Choose a tube furnace that offers a temperature range slightly higher than your requirements to allow for flexibility and future experiments.
Heating Zone Length: The length of the heating zone inside the tube furnace is crucial, as it determines the capacity to accommodate samples of different sizes. Ensure that the furnace’s heating zone is long enough to accommodate your samples comfortably.
Temperature Control and Accuracy: Look for tube furnaces with precise temperature control capabilities and high temperature accuracy. Controllers with easy-to-use interfaces and PID (Proportional-Integral-Derivative) algorithms are desirable for maintaining stable and accurate temperatures.
Heating Rate and Cooling Rate: Consider the heating and cooling rates of the tube furnace. Faster heating and cooling rates can be advantageous for time-sensitive experiments and processes.
Gas Atmosphere Compatibility: If your experiments or processes require a controlled gas atmosphere, ensure that the tube furnace can accommodate such conditions. Some furnaces offer the option for gas flow and controlled atmosphere.
Safety Features: Safety should be a priority when choosing a tube furnace. Look for furnaces with features such as overheat protection, safety interlocks, and clear indication of the hot surfaces to prevent accidents.
Material of Construction: The material of the tube furnace is essential, especially if you plan to use corrosive or reactive materials. Quartz or ceramic tubes are often used for general purposes, while high-quality alumina or other refractory materials are preferred for more demanding applications.
Size and Footprint: Consider the available space in your laboratory or workspace and choose a tube furnace that fits appropriately without causing obstruction.
Power Requirements: Check the power requirements of the furnace to ensure that your facility can provide the necessary electrical supply for the unit.
Price and Budget: Determine your budget and compare the features and specifications of different models within that range. While it’s essential to consider cost, prioritize getting a furnace that meets your requirements and offers good value for money.
Reviews and Recommendations: Read reviews and seek recommendations from peers or colleagues who have experience with the specific model or brand you are considering. Their insights can provide valuable guidance in making your decision.
By carefully considering these factors, you can make an informed decision and select a tube furnace that will serve your needs effectively and reliably.
FAQ
Q: What is the maximum temperature a tube furnace can achieve?
A: The maximum temperature a tube furnace can achieve depends on its design and specifications. Basic laboratory-grade tube furnaces typically have temperature ranges up to 1200°C, while more advanced models can reach temperatures of 1500°C, 1600°C, or even higher.
Q: What type of samples can be heated in a tube furnace?
A: A tube furnace can heat a variety of samples like powders, pellets, wires, and tubes.
Q: How long does it take for a tube furnace to reach its maximum temperature?
A: The time it takes for a tube furnace to reach its maximum temperature, known as the heating rate, can vary depending on the furnace’s power, heating element design, and size. In general, it can take anywhere from a few minutes to hours to reach the desired temperature.
Q: Can tube furnaces be used in a controlled atmosphere?
A: Yes, many tube furnaces can be operated in a controlled atmosphere by introducing specific gases into the heating chamber. This feature is valuable for conducting experiments and processes under specific environmental conditions, such as inert gas atmospheres or reducing atmospheres.
Q: How do I clean a tube furnace?
A: Cleaning a tube furnace involves several steps. First, make sure the furnace is completely cool and disconnected from the power source. Then, remove any residue or debris from the heating chamber and tube using a soft brush or compressed air. For more thorough cleaning, you can use appropriate cleaning agents based on the material of the tube furnace. Be sure to follow the manufacturer’s guidelines and safety precautions.
Q: Can I use a tube furnace for heat treatment of metals and alloys?
A: Yes, tube furnaces are commonly used for heat treatment processes of metals and alloys, such as annealing, tempering, quenching, and hardening. These processes help modify the mechanical properties of the materials and are widely used in the metallurgical industry.
Q: Can I scale up my experiments using a larger tube furnace?
A: Yes, some tube furnaces can be scaled up to accommodate larger quantities of materials or bigger sample sizes while maintaining similar heating characteristics. For industrial applications, larger tube furnaces are often used to handle higher volumes of production.
Q: How do I choose the right size of the tube furnace for my experiments?
A: When choosing the size of a tube furnace, consider the dimensions of your samples and the heating zone length required. Select a tube furnace that can comfortably accommodate your sample size and provides enough space for uniform heating. Additionally, ensure that the furnace’s footprint fits within your laboratory or workspace.