Table of Contents
Introduction
What is a Sintering Furnace?
At its core, a sintering furnace is a specialized heating apparatus engineered to facilitate the sintering process.
Sintering, a thermal treatment process, involves subjecting powdered materials to elevated temperatures below their melting point. Through carefully controlled heating, the particles within the powder compact and bond together, resulting in the formation of solid objects with desired properties.
Unlike traditional melting processes, sintering retains the integrity of the material’s structure while enhancing its density and strength.
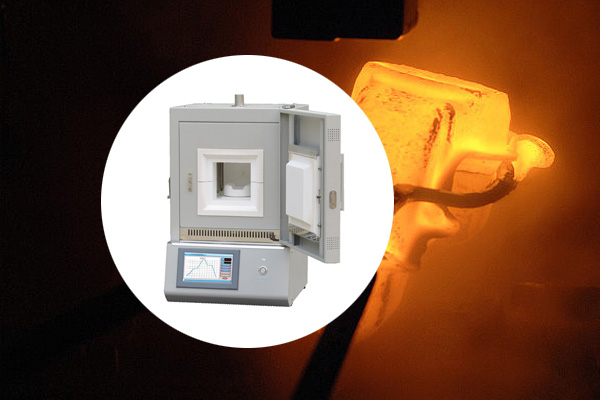
Key Points About Sintering Furnaces:
Fundamental Process: Sintering furnaces facilitate the sintering process, which involves heating powdered materials to a temperature below their melting point, causing them to bond and form solid objects.
Diverse Applications: Sintering furnaces find applications across a wide range of industries, including automotive, electronics, aerospace, medical, ceramics, and powder metallurgy.
Material Transformation: Through controlled heating, sintering furnaces enable the transformation of powdered materials into solid objects with enhanced density, strength, and desired properties.
Complex Geometries: Sintering furnaces allow for the fabrication of components with intricate geometries, offering designers and engineers greater flexibility in product development.
Customization Options: Manufacturers often offer customization options for sintering furnaces to accommodate specific industry requirements, ensuring optimal performance and versatility.
Continuous and Batch Processes: Sintering furnaces can operate in continuous or batch modes, catering to different production volumes and process requirements.
Enhanced Durability: Sintered components exhibit superior durability, wear resistance, and thermal stability, making them ideal for demanding applications in automotive, aerospace, and defense industries.
Biocompatibility: In the medical field, sintering furnaces are used to produce biocompatible implants and devices with tailored properties, ensuring compatibility with the human body.
Energy Efficiency: Advances in sintering furnace technology have led to improved energy efficiency, reducing operational costs and environmental impact.
These key points highlight the essential aspects of sintering furnaces, emphasizing their significance in modern manufacturing and material processing industries.
What is a Sintering Furnace Used For?
By enabling the fabrication of complex geometries, high-performance components, and customized materials, sintering furnaces play a pivotal role in advancing product design, functionality, and efficiency across diverse sectors. From enhancing the durability of automotive components to enabling miniaturization in electronics and ensuring biocompatibility in medical implants, sintering furnaces drive innovation and enable the realization of cutting-edge technologies.
Automotive Industry: Used for manufacturing components such as gears, bearings, brake pads, and engine parts. Sintered components offer enhanced durability, wear resistance, and precision, making them ideal for automotive applications.
Electronics and Electrical Industry: Plays a crucial role in the production of electronic components such as capacitors, resistors, and semiconductor devices. Sintering enables the fabrication of miniaturized components with precise electrical properties and high reliability.
Aerospace and Defense: In aerospace and defense applications, sintering furnaces are used to produce lightweight yet durable components for aircraft, missiles, and military equipment. Sintered materials offer superior strength-to-weight ratios, thermal stability, and resistance to harsh environments.
Medical Equipment Manufacturing: Used for manufacturing medical implants, surgical instruments, and dental prosthetics. Sintered implants offer biocompatibility, corrosion resistance, and tailored mechanical properties, ensuring compatibility with the human body.
Ceramics and Powder Metallurgy: Sintering furnaces are widely used in the production of ceramic products, advanced ceramics, and powder metallurgy components. Sintered ceramics exhibit excellent hardness, thermal resistance, and chemical inertness, making them suitable for applications in construction, electronics, and aerospace.
Research and Development: Is an essential tool for research laboratories and academic institutions to study material properties, develop new materials, and conduct experiments in metallurgy, ceramics, and materials science.
Overall, sintering furnaces play a critical role in modern manufacturing processes, enabling the production of high-quality components with precise geometries, tailored properties, and superior performance characteristics across a diverse range of industries.
Benefit
Some key benefits include:
Improved Material Properties: Sintering furnaces facilitate the creation of components with superior mechanical, thermal, and electrical properties compared to their raw powdered forms.
Complex Geometry Fabrication: Sintering furnaces enable the production of components with intricate geometries that are difficult or impossible to achieve through conventional manufacturing methods.
Cost Efficiency: Sintering can be a cost-effective manufacturing method, especially for producing components in large quantities.
Versatility: Can handle a variety of materials, including metals, ceramics, polymers, and composite materials.
Customization: Flexibility in design and customization allows manufacturers to tailor material properties and component characteristics according to specific application requirements.
Environmental Sustainability: Sintering processes typically require lower energy consumption compared to traditional manufacturing methods like casting or machining. Additionally, sintering can often be carried out in a controlled atmosphere, reducing the emission of pollutants and minimizing environmental impact.
Reduced Lead Times: Sintering furnaces enable rapid prototyping and production of components, leading to shorter lead times compared to conventional manufacturing techniques.
Images
Mini Sintering Furnace
Dental Sintering Furnace
Large Size Sintering Furnace
Sintering Furnace Price
Generally, smaller and less complex sintering furnaces may start at a few thousand dollars, while larger and more advanced models can cost tens or even hundreds of thousands of dollars.
Factors affecting sintering furnace prices:
Size and Capacity: Larger furnaces capable of accommodating larger batches of materials typically come with higher price tags due to their increased production capacity.
Heating Method: The heating method employed by the furnace, such as electric resistance, gas, or microwave, can impact the cost. Electric furnaces may be more affordable upfront, while gas or microwave furnaces may offer advantages in terms of energy efficiency but come with higher initial costs.
Additional Features and Automation: Advanced features such as programmable controls, atmosphere control systems, and automated loading/unloading mechanisms can increase the price of a sintering furnace. These features enhance efficiency, precision, and ease of operation but may add to the overall cost.
Supplier Reputation: Established manufacturers with a reputation for producing high-quality, reliable equipment may command higher prices for their sintering furnaces compared to lesser-known brands. However, investing in a reputable manufacturer can offer assurance of product quality, performance, and after-sales support.
What to Consider When Purchasing Sintering Furnace?
When purchasing a sintering furnace, several key considerations should be taken into account:
Application Requirements: Understand the intended application of the sintering furnace and the types of materials to be processed. Consider factors such as desired material properties, component size and complexity, production volume, and process parameters.
Furnace Type and Configuration: Evaluate different types of sintering furnaces, such as continuous or batch furnaces, and choose a configuration that aligns with the production needs and workflow of the facility. Consider factors such as furnace size, capacity, heating method (electric, gas, microwave), and temperature range.
Quality and Reliability: Prioritize sintering furnaces from reputable manufacturers with a track record of producing high-quality, reliable equipment. Consider factors such as build quality, durability, component materials, and adherence to industry standards and regulations.
Customization Options: Look for sintering furnace suppliers that offer customization options to tailor the equipment to specific application requirements. Consider features such as programmable controls, atmosphere control systems, automated loading/unloading mechanisms, and custom heating profiles.
Operational Efficiency: Assess the energy efficiency, productivity, and operational efficiency of the sintering furnace. Consider features such as rapid heating and cooling cycles, uniform temperature distribution, energy-saving modes, and automated process controls to optimize production efficiency and minimize downtime.
Safety Features: Ensure that the sintering furnace is equipped with adequate safety features to protect personnel and equipment during operation. Look for features such as temperature monitoring and control systems, overheat protection, gas detection systems, and emergency shutdown mechanisms.
After-Sales Support and Service: Choose a sintering furnace supplier that provides comprehensive after-sales support, technical assistance, and maintenance services. Consider factors such as warranty coverage, spare parts availability, training programs, and responsive customer support to ensure ongoing reliability and performance of the equipment.
Cost and Budget: Evaluate the overall cost of the sintering furnace, including initial purchase price, installation costs, operating expenses, and long-term maintenance costs. Compare quotes from multiple suppliers and consider the total cost of ownership over the expected lifespan of the equipment.
By carefully considering these factors and conducting thorough research, buyers can select a sintering furnace that meets their specific needs, delivers reliable performance, and provides long-term value for their investment.
FAQ
Q: How does a sintering furnace work?
A: A sintering furnace operates by subjecting powdered materials to controlled heating at temperatures below their melting point, causing them to bond together and form solid objects.
Q: What are the main types of sintering processes?
A: The main types of sintering processes include solid-state sintering, liquid-phase sintering, and pressure-assisted sintering. Each process has its own advantages and is used based on specific application requirements.
Q: What types of materials can be processed in a sintering furnace?
A: A sintering furnace is capable of processing a wide range of materials, including metals, ceramics, metal alloys, and composite materials.
Q: What is the temperature of sintering furnace?
A: The temperature of a sintering furnace can vary depending on the specific materials being processed and the desired outcomes of the sintering process. However, in general, sintering furnaces typically operate at temperatures ranging from around 600°C (1112°F) to 1600°C (2912°F) or higher. The exact temperature required for sintering depends on factors such as the composition of the materials, their particle size and distribution, and the desired densification and bonding characteristics.
Q: Can sintering furnaces be customized according to specific industry requirements?
A: Yes, many sintering furnace manufacturers offer customization options to tailor the equipment to specific industry needs, such as size, heating method, temperature range, atmosphere control, and automation features.
Q: What are the advantages of purchasing a sintering furnace from reputable manufacturers like ZYLAB?
A: Reputable manufacturers like ZYLAB offer high-quality sintering furnaces with advanced features, reliable performance, comprehensive after-sales support, and adherence to industry standards and regulations.
Q: What are the environmental considerations associated with sintering processes?
A: Sintering processes may generate emissions and waste materials that require proper handling and disposal to minimize environmental impact. Implementing efficient exhaust systems and recycling methods can help reduce environmental pollution.