Table of Contents
Sintered NdFeB permanent magnets are produced using the powder metallurgy method, involving five main stages: raw material preparation, crushing and powdering, orientation and forming, sintering and heat treatment, and machining. Each stage is further divided into several smaller steps.
Raw Material Preparation
The production of sintered NdFeB permanent magnets requires meticulous raw material preparation, which includes the following aspects:
Raw Materials
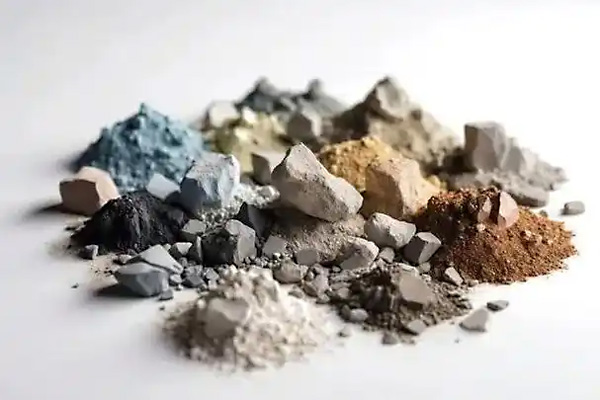
1. Selection of Rare Earth Raw Materials:
- Rare earth raw materials are typically in the form of pure metals, such as praseodymium-neodymium metal, lanthanum-cerium metal, or mixed rare earths.
- To reduce costs, rare earth alloys (such as dysprosium-iron alloys) may sometimes be used.
2. Addition of High Melting Point Elements:
- High melting point elements (such as B, Mo, Nb, etc.) are usually added in the form of iron alloys.
- These elements play a role in adjusting the grain boundary phase and optimizing the performance of the final alloy.
3. Formulation Design:
- Nd-Fe-B magnets have a multi-metal phase characteristic. To ensure high coercivity and optimized grain boundary phases, the rare earth and B content is usually higher than the stoichiometric composition.
- In certain cases (such as when adding Cu, Al, Ga, etc.), the B content may be slightly lower than the stoichiometric composition to optimize the grain boundary phase composition.
4. Purity Control:
- Raw materials must strictly control impurity content, and surface oxidation layers and contaminants must be thoroughly removed.
- When designing the formulation, the loss of rare earth metals during the melting and sintering processes must be taken into account.
Melting
1. Melting Method:
- Medium-low frequency induction melting is used (frequency 1000-2500 Hz), where alternating magnetic fields generate eddy currents to heat the raw materials.
- Electromagnetic stirring promotes the melting of un-melted raw materials and helps homogenize the melt.
2. Raw Material Size Control:
- According to the skin effect, the raw material size must be controlled to 3-6 times the skin depth (below 100mm) to ensure uniform heating.
3. Melting Temperature:
- The melting point of rare earth metals is between 800-1500°C, while high melting point metals range from 1600-3400°C.
- The melting temperature is typically controlled between 1000-1600°C, where the rare earth metals alloy with the high melting point elements during the melting process.
4. Environment Control:
- To reduce oxidation and the volatilization of rare earth elements, the melting is carried out in a vacuum (10⁻²-10⁻³) or under a high-purity argon atmosphere (pressure 50 kPa).
- The furnace must be evacuated, and gases from the raw materials and furnace components must be vented. The pressure rise rate should be below 5×10⁻⁴-1×10⁻³ L/s.
5. Continuous Feeding:
- Continuous melting-casting technology is used, with sequential feeding: first pure iron, followed by high melting point metals or alloys, and finally the rare earth materials to reduce the volatilization of rare earth elements.
6. Melting Equipment:
Click here to view more information about melting furnaces!
Pouring
-
Rapid Cooling:
- To prevent the formation of α-Fe or α-Co phases, the pouring process requires rapid cooling.
- The rapid solidification strip casting technique can cool the molten alloy into thin sheets with a thickness of 0.2-0.6mm, effectively suppressing the formation of the α phase and ensuring a uniform distribution of the Nd-rich phase.
-
Traditional Ingot Casting:
- Advantages: Simple equipment, low cost, and able to meet general magnet production requirements.
- Disadvantages: Uneven grain size and easy precipitation of α-Fe or α-Co phases.
- Improvement: Long-term low-temperature heat treatment can reduce the α phase but leads to the aggregation of the Nd-rich phase, which is not conducive to optimizing the distribution of the magnet’s grain boundary phase.
-
Strip Casting Technology:
- The molten alloy is poured onto a rapidly rotating water-cooled metal wheel through a trough, producing thin sheets with a thickness of 0.2-0.6mm.
- Advantages: Reduces the amount of rare earth elements used, lowers costs, and optimizes magnet performance.
- Disadvantages: The reduction in the Nd-rich phase increases the brittleness of the magnet and makes it more difficult to process.
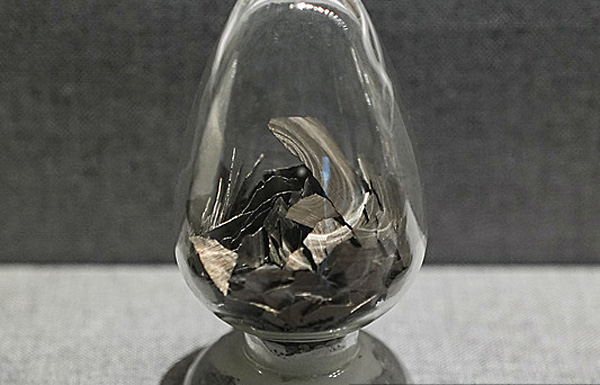
Crushing and Powder Preparation
The primary goal of powder preparation is to achieve the appropriate powder shape, average particle size, and particle size distribution.
The ideal microstructure of sintered magnets is composed of fine and uniform primary phase grains surrounded by smooth, thin additional phases, with the easy magnetization direction of the primary phase grains as consistently aligned as possible along the orientation direction.
To achieve this, the alloy ingots or rapidly cooled strips need to be processed into single crystal particles with an average particle size of 3-5μm, a maximum particle size of less than 20μm, and a shape close to spherical. Additionally, the proportion of excessively fine grains must be controlled to avoid a tendency for serious powder oxidation.
If necessary, powder surface treatment is performed to enhance its oxidation resistance and improve its filling and compressibility.
Below are three commonly used and effective methods for material crushing:
Mechanical Crushing Method
Features:
- Uses a jaw crusher or similar equipment for staged crushing to achieve the target particle size.
- Prone to introducing impurities, which can affect powder quality.
Protective Measures:
- Coarse and medium crushing are carried out under nitrogen or argon gas protection.
- Fine grinding is performed using liquid-protected ball mills or inert gas airflow mills.
Application:
- Dual-alloy or multi-alloy mixed grinding to enhance powder uniformity.
Equipment:
Hydrogen Crushing Method
- Principle: Hydrogen atoms enter the alloy grain boundaries, causing lattice expansion, increased internal stress, and triggering grain boundary or grain fractures.
- Advantages: Rapid alloy crushing with minimal mechanical damage.
Airflow Milling Method
- Principle: Uses high-pressure (0.6 MPa) high-purity nitrogen gas as the driving force to achieve particle collision and crushing through high-speed gas flow.
- Alternative Gas: Helium is more effective due to its higher flow rate (2.9 times faster than nitrogen), but it is more costly.
- Result: Can rapidly reduce powder particle size to D50 ≤ 2μm.
- Equipment:
Orientation Forming
Magnetic field orientation forming is a process that utilizes the interaction between magnetic powder and an external magnetic field to align the easy magnetization axis of powder particles with the final magnetization direction of the magnet. This is the most commonly used method for producing anisotropic magnets.
Nd-Fe-B alloy powder particles are uniaxially anisotropic, and the easy magnetization axis of each particle corresponds to the c-axis of the primary phase crystal cell.
Under the influence of an external magnetic field (≥0.8 A/m), the powder particles transform from a multi-domain state to a single-domain state, and the direction is adjusted through rotation or movement.
Pressing Forming Methods
Single-Stage Forming:
- Unidirectional Press: Pressure of 50-100 MPa, with a green body density of 55%-60% of the theoretical density.
- Cold Isostatic Press: Pressure of approximately 200 MPa, with a green body density of 60% of the theoretical density.
Two-Stage Forming:
- Unidirectional Press Pre-pressing: Pressure of 20-30 MPa, with a green body density of 45% of the theoretical density.
- Cold Isostatic Press Re-pressing: Pressure of approximately 200 MPa, with a green body density of 60% of the theoretical density.
Cold isostatic pressing is also commonly used for secondary pressing of unidirectional pressed green bodies.
When the magnetic field for orientation is limited, a lower pressure is first applied to achieve the appropriate degree of orientation. Then, isostatic pressing is used to further increase the green body density without compromising the existing orientation level.
Green body treatment
Orientation Process:
- The alloy powder maintains a good c-axis alignment.
- After pressing, the green body is demagnetized to eliminate magnetic dipole interactions and prevent orientation degradation.
- Achieve a high orientation degree in the green body.
Balance between Pressure and Magnetic Field:
- High pressures (e.g., 100MPa) may cause particle movement or rotation, reducing the orientation degree.
- It is essential to reasonably balance the magnetic field strength and forming pressure while ensuring the density of the green body.
Role of Lubricants:
- Organic lubricants are used to reduce internal friction and improve powder flowability.
- The lubricant must be completely removed before sintering (around 200°C) to avoid any negative effects on magnetic properties caused by oxidation or carbonization.
Forming Process Types and Performance Comparison
Three Forming Methods:
- Vertical Pressing (TDP): The magnetic field direction is perpendicular to the forming pressure.
- Parallel Pressing (ADP): The magnetic field direction is parallel to the forming pressure.
- Isostatic Pressing (IP): Uniform pressure is applied using mediums such as liquid or rubber.
Performance Differences:
-
Remanence and Saturation Magnetization Ratio as a Measure of Orientation:
- RIP (Rubber Mold Pressing): 94%-96%
- TDP: 90%-93%
- ADP: 86%-88%
-
Magnetic Properties ((BH)max):
- RIP > TDP > ADP, with a difference of 16-40KJ/m³ (2-5MGOe).
Recommended Forming Equipment
Click here to see more information on lab presses and tablet press molds!
Sintering and Heat Treatment
Goals and Requirements of Sintering
High Density:
- The green body, oriented by magnetic field pressing, is sintered under high vacuum or pure inert atmosphere to achieve more than 95% of theoretical density.
- After sintering, the pores in the magnet form a closed structure, improving the uniformity of magnetic flux density and the chemical stability of the metal.
Microstructure Control:
- The permanent magnetic properties of the magnet are closely related to its microstructure, and the sintering process requires fine control of the microstructure.
- While heat treatment can adjust some structural features, the key microstructure is mainly dependent on the control during the sintering stage.
Sintering Temperature and Grain Characteristics
- To prevent the main phase grains from growing too large and reducing the coercivity, the sintering temperature should be kept below 1100°C, typically controlled between 1050°C and 1080°C.
- An optimized sintering process can achieve nearly zero porosity in the actual density, with grain sizes maintained between 5-15μm.
The optimal combination of heat treatment temperature and time is closely related to the added elements and their composition in Nd-Fe-B magnets.
Importance of Two-Stage Heat Treatment
First Stage Heat Treatment:
- Temperature: Around 900°C.
- Function: Adjust the main phase grain and grain boundary structure, optimize coercivity.
- Principle: At 900°C, the Nd-rich phase is in a liquid state and acts as a grain boundary phase, repairing the surface of the main phase grains.
- Characteristics: The repair effect is not dependent on specific composition, but the treatment time must be controlled to prevent excessive growth of main phase grains or enrichment of the Nd-rich phase.
Second Stage Heat Treatment:
- Temperature: Around 500°C.
- Function: Adjust the phase composition and microstructure of the magnet, optimize the squareness of the demagnetization curve and high-temperature performance.
- Principle: In this temperature range, eutectic reactions occur, resulting in changes in the amount, composition, and distribution of the liquid phase, significantly affecting intrinsic coercivity and high-temperature irreversible losses.
After sintering and heat treatment, rapid cooling (quenching) is required to fix the formed microstructure and prevent further structural evolution.
Sintering and Heat Treatment Equipment
Click here to see more information about sintering furnaces!
Mechanical Processing
Necessity of Mechanical Processing
Shape Complexity:
- Many finished magnets are small in size and complex in shape, making it impossible to directly produce them through magnetic field orientation forming techniques. These can only be processed from the green magnet body to achieve the desired shape.
Insufficient Dimensional Precision:
- Even with near-net-shape techniques, the low powder packing density and poor flowability often result in uneven mold filling, causing fluctuations in the shape and dimensions of the green magnet body.
Sintering Shrinkage Differences:
- Nd-Fe-B magnets exhibit different sintering shrinkage rates parallel and perpendicular to the orientation direction. Additionally, there is a variation in sintering shrinkage between the edge and the center of the green body, making it difficult to meet the dimensional precision requirements for the finished product.
Comparison of Domestic and International Processes
Japanese and Western Enterprises:
- They focus on cost control, often using near-net-shape processes combined with necessary subsequent mechanical processing.
Chinese Enterprises:
- There is a wide variety of products, usually combining mechanical processing with green magnet body processing steps.
- Drawing from ceramics and crystal processing techniques, Chinese enterprises have developed a relatively high level of mechanical processing.
- With rising raw material and labor costs, near-net-shape and automated forming technologies are rapidly developing in China as well.
Characteristics of Mechanical Processing
Material Properties:
- Rare-earth permanent magnets are typical metal-ceramic products, characterized by hardness and brittleness.
Available Processing Methods:
- Common mechanical processing methods, such as turning, milling, planing, grinding, and drilling, are suitable for cutting, drilling, grinding, and honing.
Impact of Surface Defects:
- Mechanical processing can create defects on the magnet surface, reducing magnetic performance and corrosion resistance, with a more severe impact on small and thin products.
Defect Repair:
- To ensure performance, it is necessary to remove or repair the surface defect layer to remedy the situation.
Through scientific process design and strict control, sintered Nd-Fe-B permanent magnets have achieved high performance and high precision, meeting a wide range of industrial and technological needs.
ZYLAB provides various high-quality and reliable equipment for magnetic material preparation, including melting, crushing, sintering, and heat treatment equipment, to meet diverse process requirements.
For more detailed information, please contact us immediately. We offer free quotes for all products!