Table of Contents
SiC Heating Elements is widely used in various high-temperature electric furnaces and other electric heating equipment in magnetic materials, powder metallurgy, ceramics, glass, machinery and other industries.
General description
The Silicon carbide heating element is a rod-shaped nonmetallic high-temperature electric heating element made of high-quality green silicon carbide as the main raw material and processed into blank, silicified at high temperature and recrystallized.
Compared with the metal electric heating element, the element has the characteristics of high service temperature, oxidation resistance, corrosion resistance, long service life, slight deformation, convenient installation and maintenance, etc.
Our the Silicon carbide heating element adopts a new cold end production process, has excellent hot and cold end resistance ratio, saves energy and has a long service life, and avoids damage to the furnace body caused by too high cold end temperature.
Type of SiC Heating Elements
Advantage
1. Selecting high purity green SiC powder, to ensure best foundation for top quality.
2. SiC tube is extruded by 500T press machine, to ensure high density uniform through whole length.
3. Excellent resistance rate between heat zone and cold zone, to avoid over-temperature of cold zone to damage furnace body.
4. Special technology to spread a protect film on the surface of hot zone, which enhance the Antioxidant property evidently and lengthen the service life.
How to Correctly Install and Use SiC Heating Elements
1. SiC heaters are hard and brittle. Please be careful to move and install to avoid damage.
2. SiC heaters will be easy broken once be damped, so water vapor will shorten the service life of heaters. If the sintered materials is moisture, We strongly suggest that furnace have an outlet to release water vapor or other waste gases in order to protect heater’s service life.
3. In order to ensure furnace temperature and surface load of heaters evenly, please keep the resistance of SiC heaters in one furnace the same, tolerance within +/-10%.
4. When furnace start to run, please raise voltage slowly and gradually, forbid to give full voltage at the beginning. Otherwise, SiC heaters will be broken by big electric current.
5. The white parts of both SiC heaters’ ends are spray aluminium, to decrease the resistance at the connection place of clamps & strips to SiC heaters. Be sure the aluminium parts not be damped.
6. Please be sure to make clamps and strips to contact Aluminium parts firmly and sufficiently. Otherwise, it’s very easy to fire at the connecting part, then to damage SiC heaters.
7. The diameter of a piercing hole drilled through the furnace wall should be about 1.5 times the diameter of cold zone. Install SiC heaters at the center of the piercing hole, and lightly pack ceramic fibre around the terminals as following drawing. If the piercing hole is too tight to the heaters, it’s easy to break heating elements during heating.
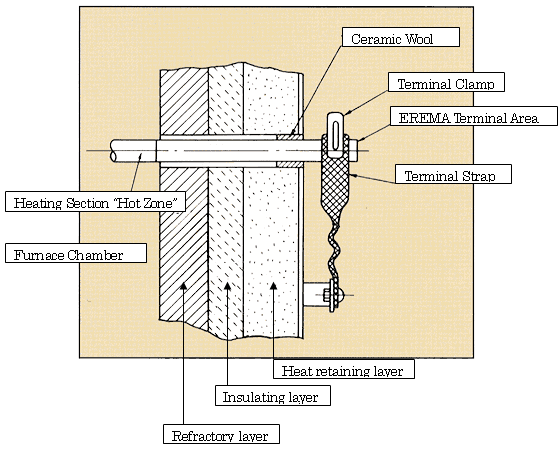
Properties
Physical properties of sic elements
specific gravity | Bend strength | hardness | Tensile strength | porosity rate | Radiancy |
2.6-2.8g/cm³ | >300kg | >9MOH’S | >150kg/cm³ | <30% |
0.85 |
The linear expansion coefficient, thermal conductivity and specific heat of the silicon carbide electrothermal element vary with temperature. The relevant data are as follows:
Temperature | Linear expansion coefficient | Heat conductivity | Specific heat |
(℃) | (10-6m/℃) | (kcal/M hr℃) | (cal/g ℃) |
0 | / | / | 0.148 |
300 | 3.8 | / | / |
400 | / | / | 0.255 |
600 | 4.3 | 14-18 | / |
800 | / | / | 0.294 |
900 | 4.5 | / | / |
1100 | / | 12月16日 | / |
1200 | 4.8 | / | 0.325 |
1300 | / | 10月14日 | / |
1500 | 5.2 | / | / |
Chemical Properties of elements
1.Antioxidant property of elements
Components in the air used to 800 ℃ began to oxidize, the temperature reached 1000- 1300 ℃, the surface of the heat generated a layer of silica protection film, 1300 ℃ crystallization of the square quartz, at 1500 ℃, the protective film reached a certain thickness, which is the component of the oxidation rate becomes extremely slow, tends to stabilize.
If it continues to heat up to more than 1627 ℃, the protective film is destroyed and the oxidation rate increases significantly, causing premature component damage.
Although the component oxidizes very slowly during use, it will still lead to an increase in resistance value after a long period of operation. This phenomenon is called aging.
In order to slow down the aging rate, we applied a protective layer on the surface of the heating part with unique technology in the manufacturing process, obviously enhancing the anti-oxidation performance of the components and prolonging the service life.
2. The effects of alkali and alkaline oxide to elements
At about 1300 ℃, alkali and alkali metal oxide react with silicon carbide to form silicate, called alkali chemical attack, which will obviously affect the red heat degree of element heating.
3. The effects to elements from melting metal
Some metals, such as cobalt, nickel, cadmium and so on, can corrode the components in the melting state at high temperature and affect the life of the components.
Element properties of elements
The the Silicon carbide heating element has a large specific resistance, and when heated in air and the surface temperature of the heating part of the element reaches about 1050 ℃, the resistivity is 600 – 1400 m ㎡ / m .
The resistance value of the element changes with the increase of temperature, from room temperature to 800 ℃ is negative, and above 800 ℃ is a positive characteristic curve.
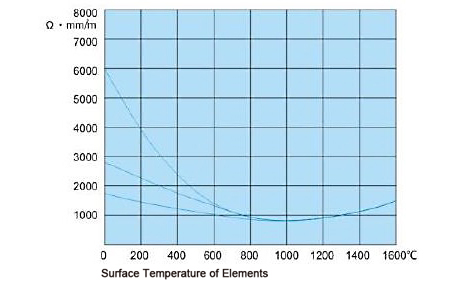
Control of applied temperature and surface load of SiC heating elements different atmosphere
Atmosphere | Furnace temp (℃) | surface load (w/c ㎡) | Acting to the element | Solve way |
Ammonia | 1290 | I | Acting on sic to form thus decrease sio2 protective film | Active at dew point |
CO2 | 1450 | 3.1 | Attack sic | protecting by quartz tube |
18%CO | 1500 | 4 | No action | |
20%CO | 1370 | 3.8 | Adsorbing C and decreasing sio2 protective film | |
halogen | 704 | 3.8 | Attacking sic and decreasing sio2 protective film | protecting by quartz tube |
hydrocarbon | 1310 | 3.1 | Adsorbing C grains causes hot pollution | Fill with enough air |
hydrogen | 1290 | 3.1 | Acting on sic to form thus decrease sio2 protective film | Active at dew point |
methane | 1370 | 3.1 | Adsorbing C grains causes hot pollution | |
N | 1370 | 3.1 | Acting on sic to form thus decrease sio2 protective film | |
Na | 1310 | 3.8 | Attack sic | protecting by quartz tube |
SO2 | 1310 | 3.8 | Attack sic | protecting by quartz tube |
vacuum | 1204 | 3.8 | ||
oxygen | 1310 | 3.8 | Sic is oxided | |
Water (different content) | 1090-1370 | 3.1-3.6 | Acting on Sic forms hydtate |
Recommend surface load
Furnace Temp | 1100 | 1200 | 1300 | 1350 | 1400 | 1450 |
Surface load of hot zone(W/c ㎡) | <17 | <13 | <9 | <7 | <5 | <4 |
Proper selection of the surface load of components according to the structure, atmosphere and temperature of the furnace is the key to achieving the best service life.
The following shows the relationship between furnace temperature, element temperature and surface load of element radiation without obstruction.
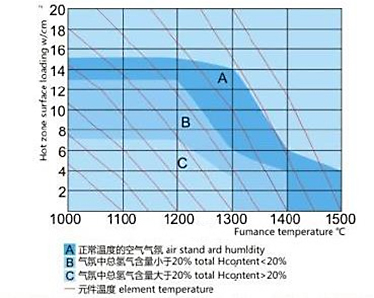
Accessories of elements
The accessory of the high-temperature electric heating element comprises a connecting belt and a fixing fixture, wherein the connecting belt is made of high-purity aluminum through a special process and is used for connecting rods and rods, rods and power supplies, plays a conductive role, and has the characteristics of good conductivity, small line loss, oxidation resistance and the like.
The fixing fixture is made of stainless steel and processed by a special process, so that the fixing rod body does not fall off and shake, and the fixing rod body is tightly connected with the connecting wire, thus ensuring the normal energization and heating of the rod body.
Standard accessories for the Silicon carbide heating elements include aluminum weaving, aluminum foil connecting strips and fixing fixtures, the specifications of which are M, C and G.
M – shaped fixed card: large elasticity and easy installation.
C – type fixed card: small occupied space and small surface tension, which needs to be installed with clamp spring pliers.
G – type fixed card: small occupied space locked by one screw, small expansion coefficient of power supply and good fixity in long-term use.
Aluminum braided connecting belt: the surface of aluminum braided belt is smooth, bright, soft, easy to dissipate heat, resistant to bending and convenient to install.
Aluminum foil connecting tape: aluminum foil tape has smooth and bright surface, good conductivity and low line loss.
Single / double – ring connecting belt: single – ring connecting belt is mainly used for connecting silicon carbide rod components to power supply; The double-ring connecting belt is mainly used for connecting the silicon carbide rod element and the element.
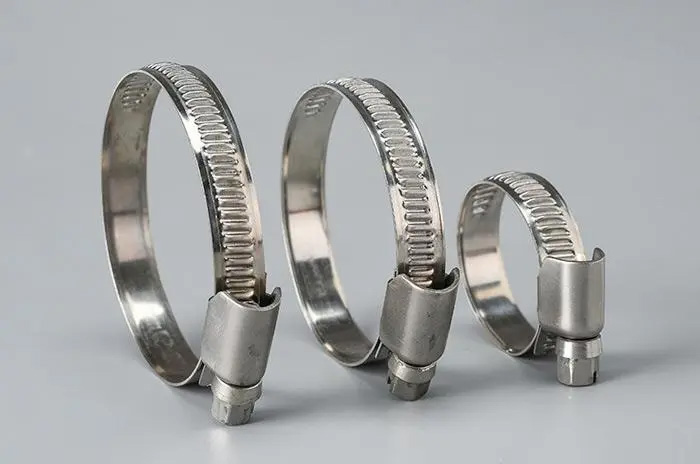
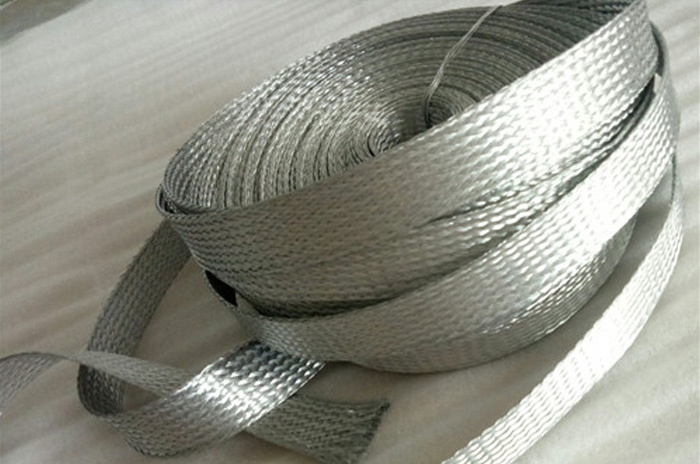
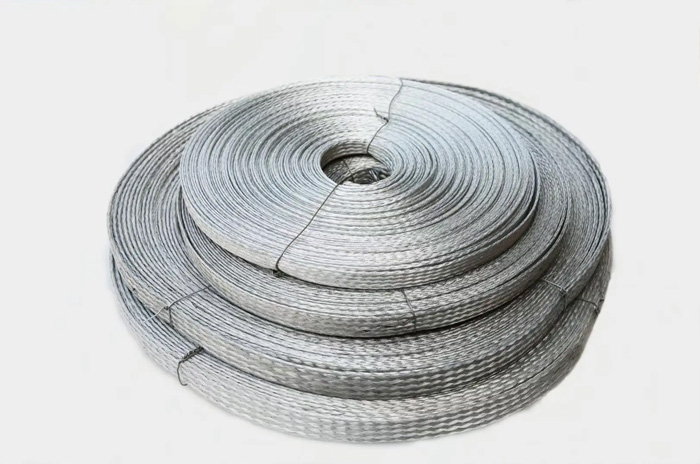
Special fixture for threaded rod, the connecting strip has conductive function, the fixing block has fixed insulation function ( positive and negative electrodes are isolated ), and the throat hoop is fixed and locked to ensure good contact between the connecting strip and threaded rod.
The aluminum woven belt is made of high purity aluminum wire woven by special process, and can be customized into connecting belts of different lengths and also sold in coils.
Installation and operation of elements
1. in order to ensure the furnace temperature and the conformity of each component to be uniform, the components should be matched with resistance before installation, and the resistance error of each group of components should be controlled below ± 5.
2. Due to the brittleness of silicon carbide components, care should be taken during installation and maintenance to avoid damage.
3. When the furnace starts to run with electricity, step up the voltage slowly, and do not fill up the load at one time, otherwise the components will be damaged due to excessive impact current.
4. The use of components must be equipped with voltage regulating transformer or silicon controlled voltage regulator and voltage, ammeter and temperature automatic control instrument, etc. During use, the resistance gradually increases due to the oxidation of components.
In order to keep the furnace temperature normal, the service voltage should be increased. When the voltage is raised to the maximum limit of the transformer used, it still cannot meet the requirements, it can stop the furnace and change the wiring mode of the components before continuing to use.
5. In the long-term use of the furnace, when individual components are damaged due to some reason and need to be replaced, the components with appropriate resistance should be selected and replaced according to the increase of the resistance of the components at that time, and no new components can be replaced at will.
If the components are damaged more or the resistance value increases too much, it is better to replace them all with new ones when the required furnace temperature cannot be reached. The replaced components will be used again ( voltmeter and ammeter ) to measure their resistance value, and the matching resistance will be used in the low temperature area.
6. New furnaces or furnaces that have not been used for a long time must be baked before they are used, and old components or other heat sources should be used as much as possible.
7. If moisture is discharged during the heating process when firing devices or materials, the furnace should be provided with vent holes to discharge moisture or other harmful waste gas from the furnace so as not to affect the service life of the components.