Chamber Furnaces
ZYLAB Chamber Furnaces are precision heating devices used for a variety of high-temperature applications, including sintering, annealing, and heat treating metals, ceramics, and other materials. They feature a sealed chamber that ensures uniform heating and precise temperature control.
These furnaces are widely used in industries for metal and alloy heat treatment, ceramic and glass sintering, material testing, and sample preprocessing. They are also valuable tools for educational and research purposes in universities and laboratories.
ZYLAB offers a range of chamber furnaces, including standard models for general applications, high-temperature versions for extreme conditions, and customized furnaces designed to meet specific client requirements such as temperature chamber capacity and working with controlled atmosphere environment such as Argon, Nitrogenetc inert gas.
For more information or to discuss a tailored solution, please contact us. Our team is at your service!
Looking for Replacement
Parts? Click Here
100-1200.C
100-1200.C
500-1500.C
100-1200.C
100-1200.C
100-1200.C
100-1200.C
Why Choose US ?
- Professional Supplier
- Large Stock
- Fast Delivery
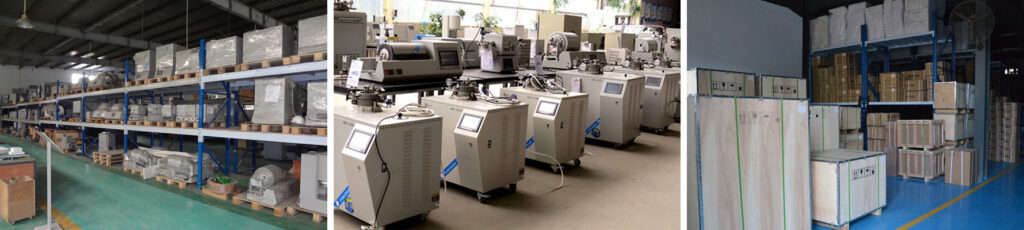
Chamber Furnace – FAQ
A chamber furnace is an industrial heating device with an insulated chamber used to heat materials to high temperatures for processes like sintering, annealing, or heat treatment. It offers precise temperature control, uniform heat distribution, and is commonly used for metals, ceramics, and polymers in various industries.
A chamber furnace heats materials in a sealed, insulated chamber using heating elements. It controls temperature precisely through a digital system, ensuring uniform heat distribution for processes like sintering or annealing. Safety features protect against over-temperature and other risks.
- Large 7″ Color Touch Panel: Easy control and programming of complex heating processes, with visual heating curves and the ability to store temperature profiles, reducing the need for repetitive adjustments.
- Durable Ceramic Fiber Chamber: Vacuum-formed for superior heat retention and longevity.
- Efficient Exhaust System: Specially designed for optimal gas flow and enhanced safety.
- Premium-Grade Heating Elements: High-quality furnace lining and high-purity heating elements for reliable performance.
- Double-Layered Steel Casing: Equipped with fan cooling for improved thermal insulation and added safety.
Chamber furnaces can be used to process a wide range of materials, including metals, ceramics, glass, polymers, and other materials requiring heat treatment, sintering, or thermal analysis, etc.
Main applications include metal annealing, ceramic sintering, plastic heat treatment, glass annealing, electronic component baking, and material testing.
Our chamber furnaces can reach up to 1200°C or 1500°C, we also offer high-temperature chamber furnaces that go up to 1700°C.
Many of our chamber furnaces can be equipped with atmosphere control systems, such as oxygen, nitrogen, hydrogen, etc., for specific heat treatment processes.
Some of chamber furnaces are designed for operation in vacuum environments, suitable for processes requiring low or no oxygen.
Regular checks of the heating elements, temperature control system, and door seals. The furnace chamber should also be kept clean.
Yes, chamber furnaces are commonly used for ceramic sintering, especially for small batch experiments or production needs.
- Versatility: Ideal for various applications, including sintering, annealing, and heat treatment, suitable for a wide range of materials.
- Compact and Efficient: Their enclosed chamber design allows for better heat retention and energy efficiency compared to other furnace types.
- Ease of Operation: User-friendly controls, programmable settings, and advanced safety features make chamber furnaces easy to use in both industrial and laboratory environments.
Our chamber furnaces are designed to minimize energy consumption by using advanced insulation materials and intelligent control systems to maximize energy efficiency.
Through high-precision temperature sensors, well-arranged heating elements, and air circulation systems, chamber furnaces maintain good temperature uniformity, with differences normally within ±5°C..
Yes, chamber furnaces are suitable for chemical reactions that require high temperatures and specific atmospheres, commonly used for material synthesis and calcination processes.
When selecting a chamber furnace, consider factors such as the type of material being processed, temperature requirements, atmosphere needs, chamber size, control system, and usage frequency.
The choice depends on the sample size and batch requirements. We offer chamber furnaces with varying chamber capacities, from 1L to 640L.
Our chamber furnaces utilize three types of high-performance heating elements:
- High-Quality Resistance Wire
- High Purity Silicon Carbide (SiC) Heating Elements
- High Purity Molybdenum Disilicide (MoSi₂) Heating Elements
Each type is selected for its durability and efficiency, ensuring reliable and consistent heating performance.
Sure, our chamber furnaces feature an 7” intelligent touch screen programmable controllers for multi-step heating, holding, and cooling processes.
The heating rate range from 1°C to 20°C per minute.
Temperature is controlled through intelligent touch screen controllers, offering precise temperature settings and automated ramping profiles.
Our chamber furnaces use high-quality vacuum formed ceramic fiber insulation to minimize heat loss and improve energy efficiency.
Our chamber furnaces are equipped with over-temperature protection, power failure protection, thermocouple disconnection alerts, and other safety mechanisms to ensure safe operation.
The heating time depends on the furnace model, size, and temperature setting. Typically, our chamber furnaces can reach their maximum temperature within a few hours to several dozen hours.
Yes, our chamber furnaces feature user-friendly controls, intuitive interfaces, and clear instructions, making them easy to operate even for those with limited experience.
Our engineers can assist you in selecting the best chamber furnace based on your specific requirements, including material type, temperature range, and processing needs.