Table of Contents
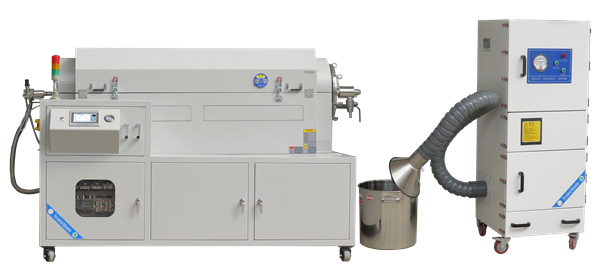
Calcination heat treatment technology for powder materials is a key material preparation process widely used in the production of lithium battery materials, ceramics, catalysts, magnetic materials, and high-performance alloys.
Through high-temperature heating, calcination induces physical or chemical changes in powder materials to achieve specific structures, phase transitions, and properties.
Purpose of Calcination
Structural Phase Transformation: Alter the crystal structure of the powder to form a stable crystalline phase.
Impurity Removal: Decompose organics and crystalline water in the powder to increase purity.
Particle Size Control: Control particle growth and sintering through calcination to achieve uniform particle size.
Performance Enhancement: Improve characteristics like chemical stability, thermal stability, and conductivity of the powder.
Powder Calcination Process
Pre-Treatment
Powder Preparation: Ensure particle size and shape meet requirements before calcination, using crushing, grinding, or sieving as needed.
Ingredient Mixing: Prepare the required chemical components based on the target material properties and mix them evenly in the correct proportions.
Shaping (if necessary): In some processes, powders may need to be pressed into shapes to facilitate calcination.
Loading into Furnace
Loading Method: Options include tray loading, fluidized bed loading, or coating the rotary furnace inner wall to ensure uniform powder distribution.
Protective Atmosphere: For oxygen-sensitive or easily oxidized materials, select a suitable protective gas (such as nitrogen or argon) to fill the furnace and prevent oxidation or adverse reactions.
Heating and Calcination
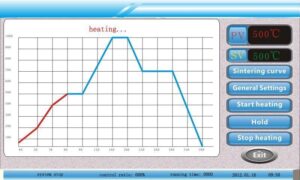
Heating Rate: Set an appropriate heating rate to avoid particle agglomeration or cracking, usually around 5-15°C/min, depending on the material.
Calcination Temperature: Set the temperature according to material properties, typically between 800-1500°C. Low temperatures may lead to insufficient calcination, while excessive temperatures could cause sintering or agglomeration.
Holding Time: Adjust the holding time based on reaction rate and particle size, usually ranging from several hours to tens of hours to ensure complete reaction and sintering.
Cooling
Rate: After calcination, cool slowly to prevent thermal shock or internal stress, usually at a rate of 5-10°C/min.
Cooling Atmosphere: For materials prone to oxidation, maintain a protective atmosphere during cooling to prevent oxidation reactions.
Post-Treatment
Crushing and Screening: After calcination, further crushing and screening may be required to achieve a specific particle size and distribution.
Surface Modification: In some cases, apply surface coating or modification to the powder to meet downstream application requirements.
Quality Control
Calcination Effect Check: Test the material’s phase structure, grain size, and specific surface area to ensure they meet design requirements.
Atmosphere Control: Check the control of the calcination atmosphere, especially for the protective gas, to ensure the material has not been contaminated by external air.
Key Control Parameters and Precautions
Temperature Accuracy: Temperature control accuracy greatly impacts calcination quality; usually, accuracy within ±1°C is required.
Atmosphere Purity: The protective atmosphere purity should reach 99.99% or higher to prevent oxidation and contamination by impurities.
Equipment Stability: Use equipment such as rotary calcination furnaces or fluidized bed furnaces with effective heat transfer and atmosphere control to achieve uniform calcination.
Atmosphere Control
Oxidizing Atmosphere: Suitable for materials that require oxidation, such as alumina and lithium battery cathode materials.
Reducing Atmosphere: By introducing hydrogen or ammonia decomposition gas, it is suitable for preparing metal powders or reduction-sensitive materials.
Inert Atmosphere: Introduce nitrogen or argon to prevent oxidation or other chemical reactions, ideal for oxygen-sensitive materials.
Common Equipment for Powder Calcination
Rotary Kiln
Suitable for large-scale powder materials, ensures uniform heating and calcination, and facilitates batch operations.
Fluidized Bed Furnace
Suspends powder in a hot gas stream for efficient, uniform heating, ideal for fine particle calcination.
Atmosphere Furnace
Used for calcination in specific atmospheres, capable of providing reducing, inert, or oxidizing atmospheres.
Box-Type Resistance Furnace
Suitable for small-batch calcination, mainly used in laboratory settings.
Application Cases
Lithium Battery Materials: Cathode materials such as lithium iron phosphate (LiFePO₄) and lithium nickel cobalt manganese oxide (NCM) are calcined to enhance electrochemical performance and thermal stability.
Ceramic Materials: Calcination of ceramic powders like alumina and zirconia improves density and mechanical properties, suitable for producing high-strength ceramic components.
Magnetic Materials: Ferrite materials are calcined to enhance magnetic properties, widely used in electronic devices.
Catalyst Carriers: Materials like alumina and titania gain excellent thermal stability and catalytic activity after calcination.
Common Issues and Solutions in the Calcination Process
Powder Agglomeration: Use dispersants, lower temperature, or employ a rotating furnace.
Over-burning or Under-burning: Optimize temperature and time, gradually increase temperature.
Atmosphere Control Issues: Select the appropriate atmosphere based on material requirements and adjust gas flow.
Uneven Temperature Distribution: Use a rotary kiln or improve furnace chamber design.
Cracking Due to Thermal Stress: Control heating/cooling rates, apply slow cooling.
Incomplete Oxidation or Reduction: Extend holding time, increase gas purity.
Equipment Contamination or Corrosion: Use corrosion-resistant materials and regularly clean equipment.
The calcination heat treatment technology for powder materials is a crucial method for optimizing material performance and controlling structure. By precisely managing temperature, atmosphere, and time parameters, this technique effectively enhances the quality and properties of powder materials, supporting their wide applications in electronics, batteries, ceramics, catalysis, and more.
Share this entry
You might also like