Table of Contents
Introduction
What is a Pellet Press?
A pellet press, also known as a tablet press, is a machine used to convert powdered or granular raw materials into solid pellets or tablets through compression and extrusion. It is commonly employed in the manufacturing of pharmaceutical tablets, pellets, caplets, or block-shaped products, possessing the capability to compress raw material powders or granules into specific shapes and densities.
A laboratory pellet press is specifically designed for sample preparation at laboratory scale. It features precise control functions, allowing for adjustments of parameters such as pressure, temperature, and compression speed to meet various experimental requirements.
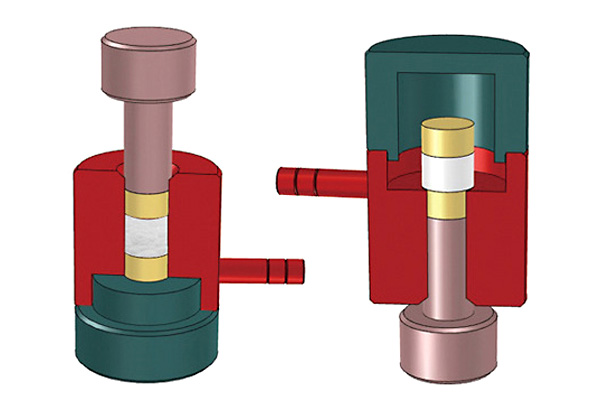
Components of a Pellet Press:
Mainframe: The main body of the pellet press, comprising the frame, base, and pressing system. It provides support and stability, while containing the control devices and actuators of the pressing system.
Pressing System: A system used to apply pressure, typically consisting of a hydraulic system, pneumatic system, or mechanical pressure system. The design of the pressing system depends on the working principle and pressing requirements of the pellet press.
Die: A molding component used to shape the pellets, available in various shapes and sizes depending on the product’s requirements.
Feeding Device: A device used to feed the raw material powder or granules into the pellet press, typically including a feeding port, feeder, and hopper.
Control System: A system used to control various operations and parameters of the pellet press, including electrical control systems, hydraulic control systems, or pneumatic control systems. The control system enables precise adjustment and monitoring of parameters such as pressure, temperature, and compression speed.
Heating or Cooling Device (optional): Depending on requirements, the pellet press may be equipped with a heating device or cooling device to adjust the temperature of the raw material during the pressing process to achieve specific pellet effects.
Safety Devices: Devices used to ensure the safety and stability of the pellet press during operation, including protective covers, safety switches, emergency stop buttons, etc.
Auxiliary Equipment: Depending on specific requirements, various auxiliary equipment may be equipped, such as dust removal systems, waste recycling devices, etc., to improve the efficiency and environmental friendliness of the pellet press.
Working Principle of a Pellet Press:
The working principle of a pellet press is primarily based on the compression principle in mechanics and the plastic deformation characteristics of materials in solid mechanics. The basic working principle can be summarized as follows:
Material Loading: To produce pellets, the desired raw material powder or granules are first loaded into the pressing die of the pellet press.
Application of Pressure: The pellet press is activated, and the pressing system begins to apply pressure to the mold filled with the raw material. The magnitude of the pressure depends on the requirements of the product being manufactured, usually ranging from hundreds to thousands of kilograms.
Material Plastic Deformation: As the applied pressure increases, the raw material powder or granules begin to undergo plastic deformation. During this process, the gaps between the material particles gradually decrease, and internal friction between particles increases.
Particle Bonding: With the increase in pressure, the friction and deformation between the material particles generate strong bonding forces, gradually forming solid pellets.
Pellet Formation: Under continuous applied pressure, the raw material particles are gradually compressed and densified until they reach the desired shape and density. This process usually takes some time and is influenced by factors such as the nature of the raw material and pressing parameters.
Pressure Release: After pellet formation is completed, the applied pressure is stopped, and the pressure in the pressure system is released. At this point, solid pellets have formed and can be removed from the mold.
Application
What are the uses of a laboratory pellet press?
Laboratory pellet presses have wide-ranging applications across multiple industries and fields, primarily including but not limited to the following aspects:
Materials Science and Engineering: Laboratory pellet presses are vital equipment in the field of materials science and engineering. They are used to prepare various types of material samples, including metals, ceramics, plastics, composite materials, etc., for material performance testing, structural analysis, prototype preparation, etc.
Chemistry: In chemical research and experiments, laboratory pellet presses are commonly used to prepare pellet samples of compounds, such as catalysts, electrode materials, pharmaceutical formulations, etc.
Geology and Mining: Laboratory pellet presses are often used in the fields of geology and mining to prepare rock, ore, and soil samples for analysis, measurement, and evaluation.
Materials Characterization and Analysis: Samples prepared by laboratory pellet presses can be used for material characterization and analysis techniques such as scanning electron microscopy (SEM), X-ray diffraction (XRD), Raman spectroscopy, transmission electron microscopy (TEM), etc.
Energy Sector: In the energy sector, laboratory pellet presses are used to prepare electrode materials for batteries, fuel cells, solar cells, as well as to research energy storage materials, photocatalysts, etc.
Medicine and Biology: In medical and biological research, laboratory pellet presses can be used to prepare drugs, biological samples, tissue samples, etc., for drug release performance testing, cell culture, tissue engineering, etc.
Food and Agriculture: Laboratory pellet presses are also applied in the food and agriculture sectors for preparing samples of food ingredients, feed, agricultural products, etc., for quality analysis, safety assessment, etc.
Role of Pellet Press in Material Sample Preparation
Pellet presses play a crucial role in material sample preparation, especially in laboratory and research environments. Here are the main functions of pellet presses in material sample preparation:
Sample Preparation: Pellet presses are used to compress raw materials (such as powders, granules, sheets, etc.) into samples of desired shapes and sizes, including discs, squares, blocks, films, etc.
Densification: By applying high pressure, pellet presses can tightly compress particles in the material together, thereby increasing the density and strength of the sample.
Shape Control: Pellet presses can precisely control the shape and size of samples as needed, such as thickness, diameter, aspect ratio, etc., ensuring that the samples meet experimental requirements.
Improvement of Material Properties: Samples prepared by pellet presses can improve the mechanical, thermal, and electrical properties of materials, meeting the requirements of specific applications.
Preparation of Composite Materials: Pellet presses can be used to press different types of materials together to prepare composite materials, such as metal matrix composites, ceramic matrix composites, etc.
Preparation of Standardized Samples: Pellet presses can be used to prepare standardized samples for quality control, performance testing, and comparative studies.
Role of Pellet Press in Electrode Material Preparation
Pellet presses play an important role in the preparation of electrode materials, especially in energy storage and conversion devices such as batteries, supercapacitors, and fuel cells. Here are the main applications of pellet presses in electrode material preparation:
Electrode Preparation: Pellet presses are used to prepare electrode sheets by uniformly mixing active materials, conductive agents, and binders, then pressing them into shape. These electrode sheets typically have specified shapes and sizes, such as discs, squares, or rectangles.
Increased Electrode Density: By high-pressure pressing, the density of active materials in the electrode can be effectively increased, improving the charge-discharge performance and cycle stability of the electrode.
Improvement of Electrode Structure: Pellet presses can compress electrode materials tightly together to form a uniform and dense electrode structure, thereby improving the conductivity of electrons and ions, reducing resistance, and improving energy storage and release efficiency.
Control of Electrode Thickness: By adjusting the parameters of the pellet press, such as pressure and time, the thickness of the electrode can be precisely controlled to meet the requirements of different applications.
Preparation of Composite Electrodes: Pellet presses can laminate layers of electrodes made of different materials to prepare composite electrodes, such as bipolar batteries and supercapacitors.
Research and Development: Pellet presses provide researchers with a convenient tool to explore new electrode materials, new processes, and new structures to improve the performance and stability of batteries and capacitors.
Benefit
Laboratory pellet presses offer numerous advantages in scientific research and laboratory applications. Here are some of the main advantages:
Precise control of pressure and temperature: Laboratory pellet presses allow precise control of the pressure and temperature applied to samples, which is crucial for material preparation and property research under laboratory conditions.
High adjustability: These devices typically feature adjustable parameters such as pressure, temperature, and pressing speed, making them suitable for various types and sizes of samples and different experimental requirements.
Batch production capability: Laboratory pellet presses can be used for batch production of samples, thereby increasing laboratory efficiency and output.
Reproducibility and consistency: By precisely controlling experimental conditions, laboratory pellet presses can achieve high reproducibility and consistency in sample preparation, ensuring the accuracy and reliability of experimental results.
Versatility: Laboratory pellet presses typically come with various functions and accessories, allowing for the preparation of different types of samples such as pellets, granules, powders, etc.
Time and cost-saving: Using laboratory pellet presses can save time and costs associated with sample preparation, while also reducing the demand for manpower and enhancing laboratory efficiency.
Ease of operation: Most laboratory pellet presses are designed to be simple and easy to operate, requiring minimal training to use effectively.
Reliability and durability: Laboratory pellet presses are usually made from high-quality materials, offering excellent durability and stability for long-term reliable operation.
Image for Pellet Press
Price
The price of pellet presses varies depending on factors such as model, specifications, brand, and features. Generally, laboratory-scale pellet presses have relatively lower prices compared to large industrial-grade ones.
Specifically, laboratory pellet press prices may range from a few thousand dollars to tens of thousands of dollars, depending on factors such as equipment specifications, features, and brand. Typically, basic models of laboratory pellet presses have lower prices, while high-end models with more features and advanced technology have higher prices.
It is important to note that the price of laboratory pellet presses may vary depending on the region, market demand, and procurement channels. When choosing a pellet press, besides price, factors such as equipment performance, quality, after-sales service, and technical support should also be considered to ensure the selection of suitable equipment that meets your needs.
It is advisable to contact relevant suppliers or manufacturers to inquire about detailed pricing information based on specific requirements and budget. Additionally, conducting market research and comparisons can provide more pricing information to make a more informed decision.
What to Consider When Purchasing Pellet Press?
When purchasing a pellet press, several important factors should be considered:
Application requirements: Firstly, determine your application requirements, including sample types, production scale, required pressure, and temperature range.
Pelleting capacity: Consider the pressure range and maximum pressure capacity of the pellet press to ensure it meets the requirements for pelleting your samples.
Pelletizing area size: Choose a pellet press with a suitable pelleting area size based on your sample size and shape requirements.
Control system: Consider the control system of the pellet press, including pressure control, temperature control, and pelletizing speed control functions.
Durability and stability: Select a pellet press with good durability and stability to ensure long-term stable operation and minimize maintenance and repair costs.
Safety: Consider the safety features of the pellet press, including safety protection devices and emergency stop buttons, to ensure the safety of operators.
Brand and manufacturer reputation: Choose pellet presses produced by reputable manufacturers and well-known brands to obtain higher quality products and more reliable after-sales service.
Price and budget: Lastly, consider the price and budget. Choose a pellet press with good value for money based on your budget and performance requirements to ensure you get the best performance and quality within your budget.
FAQ
1. Uneven or insufficient compaction:
Possible reasons: Improper parameter settings of the pellet press, uneven distribution of raw material powder, damaged mold, etc.
Solution: Adjust the parameters of the pellet press, refill the raw material, replace the mold, or perform equipment maintenance.
2.Insufficient compaction pressure or failure to reach the preset pressure:
Possible reasons: Insufficient pressure in the hydraulic system, hydraulic pump failure, aging of sealing elements, etc.
Solution: Check the hydraulic system, replace the hydraulic pump, replace sealing elements, or perform system debugging.
3.Mold damage or severe wear:
Possible reasons: Mold wear due to prolonged use or improper operation, poor-quality molds, etc.
Solution: Replace the mold with a new one, choose higher-quality molds, strengthen mold maintenance, etc.
4.Hydraulic system leakage:
Possible reasons: Aging of hydraulic pipelines, damage to sealing elements, hydraulic oil loss, etc.
Solution: Replace hydraulic pipelines, replace sealing elements, replenish hydraulic oil, and check the hydraulic system for leaks.
5.Inaccurate temperature control:
Possible reasons: Malfunction of temperature sensors, aging of heating elements, control system failure, etc.
Solution: Replace temperature sensors, repair or replace heating elements, adjust the control system, etc.