Table of Contents
What is Mechanical Alloying?
Mechanical alloying refers to a powder preparation technique in which metal or alloy powders are subjected to prolonged, intense impacts and collisions between powder particles and milling balls in a high-energy planetary ball mill. This process causes repeated cold welding and fracturing of the powder particles, leading to atomic diffusion within the powder particles and resulting in alloyed powders.
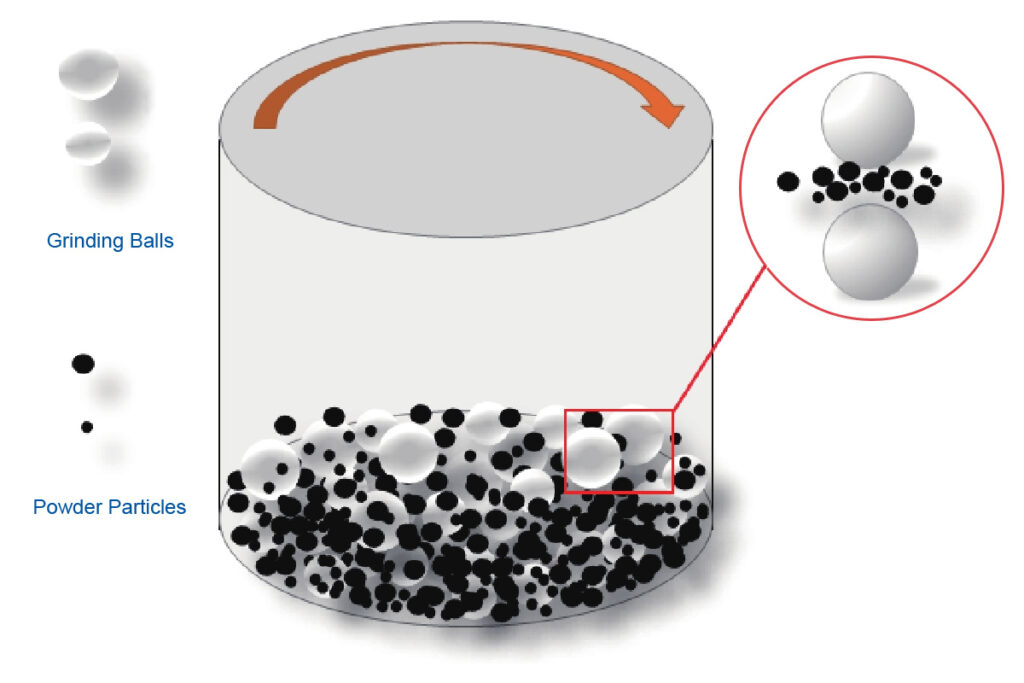
Mechanical alloyed powders are not like alloy materials formed after melting and casting metals or alloys, where the components fully achieve atomic-level bonding to form a uniform solid solution or compound.
In most cases, within a limited milling time, the components only reach or approach atomic-level distances at points, lines, and surfaces where they come into contact. The final product is typically a mixture or composite with very uniformly distributed components.
However, in some systems, with extremely long milling times, atomic-level bonding and the formation of alloys or compounds can occur through solid-state diffusion.
Factors Affecting Mechanical Alloying:
Mechanical alloying is a complex process, and achieving the desired phases and microstructures requires the careful optimization of several influencing parameters. Below are some of the parameters that significantly impact the results of mechanical alloying.
Grinding Equipment
There are various types of grinding equipment used to produce mechanically alloyed powders, such as planetary mills, vibratory mills, and stirred mills.
These devices differ in terms of grinding energy, grinding efficiency, material contamination levels, and the forces between the grinding media and the inner wall of the grinding jar, all of which critically affect the grinding results.
The material and shape of the grinding jar significantly influence the outcome as well.
During the grinding process, the impact and friction of the grinding media against the inner wall of the grinding container can cause a portion of the material from the container wall to detach and contaminate the ground material.
Commonly used grinding jars are typically made from hardened steel, tool steel, stainless steel, PK5; lined with hardened steel or hard alloys, etc. Sometimes, special materials are selected for specific purposes; for example, when the ground material contains copper or titanium, copper or titanium grinding jars are used to minimize contamination.
Grinding Speed
The higher the speed of the mill, the more energy is transferred to the grinding material. On the other hand, excessively high speeds can cause the grinding system to heat up too quickly, leading to excessively high temperatures, which can sometimes be detrimental.
For example, higher temperatures may cause the decomposition of supersaturated solid solutions, amorphous phases, or other metastable phases that are required to form during the process.
Grinding Time
Grinding time is one of the important factors affecting the results. Under certain conditions, as grinding progresses, the degree of alloying increases, and the particle size gradually decreases until a stable equilibrium state is reached, where cold welding and fracturing of particles achieve dynamic balance, and the particle size no longer changes. On the other hand, the longer the grinding time, the more severe the contamination. Therefore, the ideal grinding time should be comprehensively determined through experimentation based on the desired outcome.
Grinding Media
When selecting grinding media, it is important to consider not only their material and shape, such as spherical or rod-shaped, similar to the grinding jar, but also their density, size, and distribution.
The grinding media should have an appropriate density and size to provide sufficient impact force on the material being ground. These factors directly affect the final product. For example, when grinding a Ti-Al powder mixture, using grinding balls with a diameter of 15 mm can result in a solid solution, whereas using grinding balls with a diameter of 25 mm will not produce a Ti-Al solid solution, even with a longer grinding time under the same conditions.
Ball-to-Material Ratio
The ball-to-material ratio refers to the weight ratio of the grinding media to the material being ground. Since the grinding media is usually spherical, it is called the ball-to-material ratio.
In experimental studies, the ball-to-material ratio used typically ranges from 1:1 to 200:1, with most cases around 10:1. For small-scale production or testing, this ratio can be as high as 50:1 or even 100:1.
Filling Ratio
The filling ratio of the grinding media refers to the percentage of the total volume of the grinding media relative to the volume of the grinding jar. The filling ratio of the material refers to the percentage of the loose volume of the grinding material relative to the gaps between the grinding media.
If the filling ratio is too low, productivity is low; if it is too high, there isn’t enough space for the grinding media and material to move freely, resulting in a lower impact force, which is unfavorable for the alloying process. Generally, the filling ratio of the grinding media is 60%-80%, and the filling ratio of the material is 100%-130%.
Gas Environment
Mechanical alloying is a complex solid-state reaction process, and any change in parameters such as the milling atmosphere, milling intensity, or milling time can affect the alloying process and the final product.
During mechanical alloying, collisions between the balls and between the balls and the jar convert mechanical energy into thermal energy, causing the temperature inside the jar to rise significantly. Additionally, during alloying, frequent particle refinement, defect introduction, and increased free energy make the powder more likely to react with oxygen in the milling atmosphere. Therefore, inert gases like argon are typically used as protective gases during mechanical alloying. Different milling atmospheres can have a significant impact on the alloying reaction mechanism, final product, and its properties.
The gas environment during milling is an important factor in causing contamination, so milling is generally carried out under vacuum or inert gas protection. However, in some cases, for special purposes, milling may be performed in a specific gas environment. For example, to produce corresponding nitrides or hydrides, milling can be conducted in a nitrogen or hydrogen atmosphere.
Process Control Agents
During the mechanical alloying process, there is severe agglomeration, caking, and wall adhesion of the powder, which significantly hinders the progress of the alloying process.
To mitigate these issues, process control agents such as stearic acid, solid paraffin, liquid alcohol, or carbon tetrachloride are often added during processing to reduce powder agglomeration, sticking of the powder to the balls and walls, and to minimize the wear of the grinding media and the inner wall of the grinding container. This helps in better controlling the powder composition and improves the yield of the powder.
Grinding Temperature
The final products of mechanical alloying (MA) — whether they are solid solutions, intermetallic compounds, nanocrystals, or amorphous phases — all involve diffusion, which is affected by the grinding temperature. Therefore, temperature is an important factor influencing mechanical alloying.
For example, in the Ni-50%Zr powder system, vibratory milling under liquid nitrogen cooling for 15 hours does not result in the formation of an amorphous phase; however, milling at 200°C leads to complete amorphization of the powder material, while milling at room temperature achieves partial amorphization.
The factors mentioned above are not independent of each other. For example, the optimal grinding time depends on the type of grinding, media size, grinding temperature, and ball-to-material ratio, among other factors.
Advantages of Mechanical Alloying:
When synthesizing high-melting-point alloys or intermetallic compounds, mechanical alloying avoids the high-temperature melting and solidification processes of conventional metallurgical methods, allowing alloying to be achieved at room temperature. This method results in uniformly structured and fine-grained alloys with a relatively high yield, making it an excellent method for producing alloys and new materials that are difficult to prepare using conventional techniques.