Table of Contents
Magnetic materials are substances that exhibit magnetic behavior under an external magnetic field, and their magnetic properties are primarily related to the material’s internal microstructure and atomic magnetic moments.
Based on different magnetic behaviors, magnetic materials can be classified into four categories: ferromagnetic, antiferromagnetic, paramagnetic, and diamagnetic.
Ferromagnetic materials spontaneously generate magnetic moments and align into a strong magnetic state under an external magnetic field. In contrast, antiferromagnetic materials have magnetic moments arranged in opposite directions, paramagnetic materials align along the magnetic field direction, and diamagnetic materials are hardly influenced by an external magnetic field.
Applications of Magnetic Materials in Various Industries and Fields
Electromagnetic Devices: Magnetic materials are widely used in the manufacturing of electromagnetic devices such as electric motors, generators, transformers, and inductors. Ferromagnetic materials like iron, nickel, cobalt, serving as the core components in these devices, enhance magnetic permeability, improving device efficiency.
Computers and Electronic Devices: Magnetic materials play a crucial role in computer storage devices (hard drives, magnetic tapes, etc.). Magnetic recording and storage technologies utilize the magnetizable properties of magnetic materials, ensuring reliable information storage and retrieval.
Magnetic Sensors: Magnetic materials find extensive applications in magnetic sensors and detection devices used to measure the strength and direction of magnetic fields. This is significant in navigation, geomagnetic measurements, and magnetic resonance imaging (MRI).
Medical Devices: In the medical field, magnetic materials are employed in Magnetic Resonance Imaging (MRI) devices, which use powerful magnetic fields to obtain detailed images of the human body’s interior.
Acoustic Devices: Magnetic materials are used in speakers and headphones to convert electrical signals into sound. Ferromagnetic materials serve as the magnetic components in speakers.
Magnetic Fluids: Magnetic fluids are liquids containing tiny magnetic particles and can be controlled by an external magnetic field. This material has unique applications in hydraulic systems, sealing technologies, and biomedical applications.
Manufacturing Industry Applications: Magnetic materials are widely used in the manufacturing of various magnetic tools, sensors, and fixtures, contributing to increased production efficiency.
These applications represent only a small fraction of the uses of magnetic materials in the technological and industrial sectors. With the advancement of technology, the application domains of magnetic materials continue to expand.
The Process Flow of Magnetic Material Preparation
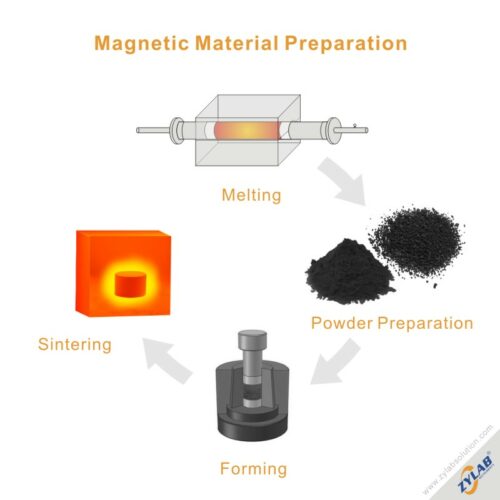
Raw Material Preparation: Select appropriate raw materials, typically metals, alloys, or oxides, based on the desired magnetic characteristics and applications. The purity and proportion of these raw materials are crucial for the final product’s performance.
Material Mixing: Uniformly mix the powdered raw materials to ensure an even distribution of various elements or compounds. This can be achieved through mechanical blending, ball milling, or other methods.
Shaping: Form the mixture into prefabricated blanks of the desired shape. Shaping methods may include pressing, injection molding, extrusion, etc.
Sintering: Subject the prefabricated blanks to a high-temperature sintering process to bond the particles into a dense structure. This step is typically carried out under controlled atmospheres to prevent oxidation or undesirable reactions.
Magnetic Treatment: Some magnetic materials may undergo special magnetic treatment steps, such as annealing or quenching under a strong magnetic field, to regulate the crystal structure and magnetic moment alignment.
Surface Treatment: For certain applications, magnetic materials may require surface treatments to enhance mechanical properties, corrosion resistance, or adhesion.
Magnetic Testing and Quality Control: Conduct magnetic tests on the prepared magnetic materials to ensure compliance with design requirements. Implement quality control measures to inspect the material’s structure, composition, and performance.
Final Processing: Depending on specific applications, perform final processing steps such as cutting, machining, coating, etc., on the magnetic materials to meet practical needs.
Recommended ZYLAB experimental equipment for magnetic material preparation:
Purification of Ferromagnetic Materials
Ore Extraction: The primary raw material for ferromagnetic materials is typically ore, such as iron ore, which is initially extracted through mining activities.
Ore Refinement: Extracted ore undergoes a refining process to eliminate impurities. This step usually involves crushing, grinding, soaking, and other treatments to transform the ore into a substance with higher purity iron.
Blast Furnace Smelting: Refined iron ore is often fed into a blast furnace, where the smelting process extracts iron from the ore. At high temperatures, chemical reactions occur between iron and other elements, forming liquid or semi-liquid metallic iron.
Steel Production: Extracted iron may require further refining and alloying, typically by mixing iron with other alloying elements like carbon, nickel, chromium, etc., to produce alloys with specific properties. Common processes include carbon steel production and electric arc furnace steelmaking.
Rolling and Shaping: Processed steel undergoes rolling and shaping to achieve the desired shape and dimensions. This step may also include heat treatment to adjust crystal structure and enhance mechanical properties.
The above steps primarily focus on ferromagnetic materials, and the purification processes for other magnetic materials may differ. For example, the preparation process of ferrimagnetic materials like magnetic iron oxide may involve steps such as solution precipitation and calcination.
Whether ferromagnetic or other magnetic materials, the goal of the purification process is to remove impurities and ensure the final material’s purity and performance meet specific application requirements.
The Role of High-Temperature Furnace in Magnetic Material Preparation
Sintering: The main function of the high-temperature furnace is sintering, where powdered magnetic materials are heated to high temperatures, causing diffusion, melting, and recrystallization between particles to form a dense structure. This helps enhance the material’s density, mechanical properties, and magnetic performance.
Diffusion of Powder Particles: In the high-temperature furnace, the powder particles of the material diffuse due to the heat, allowing atoms or molecules between the particles to migrate more easily and aiding particle bonding.
Adjustment of Crystal Structure: The magnetic performance of magnetic materials is closely related to their crystal structure. The sintering process in the high-temperature furnace can lead to adjustments in the crystal structure, aiding in optimizing magnetic performance, such as changing the size, shape, and orientation of crystals.
Removal of Volatile Substances and Moisture: At high temperatures, volatile substances and moisture in magnetic materials can be eliminated, a crucial step in the sintering process. Removing these impurities helps avoid unstable chemical reactions in the final product during high-temperature processes.
Facilitation of Particle Bonding: Under high-temperature conditions, the surface of powder particles may undergo melting or partial melting, promoting bonding between particles. This contributes to the formation of a denser and more uniform material structure.
Heat Treatment: The high-temperature furnace can also be used for the heat treatment of magnetic materials, such as annealing or quenching in a magnetic field, to adjust the material’s microstructure and enhance magnetic performance.
The high-temperature furnace plays a crucial role in the preparation of magnetic materials, allowing precise control of the structure and performance of magnetic materials by regulating temperature and atmosphere.
How to Choose the Right Melting Furnace, Sintering Furnace, and Annealing Furnace
Melting Furnace:
Material Type: Different magnetic materials may have varying requirements for melting conditions. Select a melting furnace that can provide the appropriate melting temperature and atmosphere to ensure the material melts in the right environment.
Melting Capacity: Based on production scale and required output, choose equipment with sufficient melting capacity.
Furnace Type: Given the unique characteristics of magnetic materials, it may be necessary to choose a furnace type that suits specific shapes and sizes, ensuring a uniform melting process.
Melting Speed: Consider production efficiency and choose equipment with an appropriate melting speed.
Sintering Furnace:
Sintering Temperature: Different magnetic materials may require different sintering temperatures. Ensure the selected sintering furnace can provide the required temperature range.
Atmosphere Control: Some magnetic materials are sensitive to atmosphere conditions during sintering. Select a sintering furnace with atmosphere control functionality to prevent adverse reactions.
Sintering Time: Based on material characteristics and desired sintering effects, choose an appropriate sintering time.
Uniform Heating: Ensure the sintering furnace has good uniform heating to avoid temperature gradients in the material, affecting the uniformity of the final product.
Annealing Furnace:
Annealing Temperature: Choose equipment that can provide the required annealing temperature to adjust the material’s crystal structure and properties.
Annealing Time: Based on specific requirements, select an appropriate annealing time to achieve the desired crystal structure adjustments.
Atmosphere Control: For some magnetic materials, especially those prone to oxidation, choose an annealing furnace with atmosphere control functionality to prevent undesirable oxidation reactions.
Cooling Speed: Consider the cooling speed after annealing to ensure the material achieves the desired physical and magnetic properties.
Here are several high-temperature furnaces recommended by ZYLAB for your reference:
When selecting these furnace types, it is advisable to consult our technical personnel first to ensure that the chosen equipment meets the specific requirements of the magnetic materials, achieving the best preparation results.