Table of Contents
What is a Feed Pump?
A feed pump is a device used to transport liquids or other fluids, typically moving materials from one container or location to another.
It plays a critical role in various industrial processes and laboratory operations, ensuring that materials are delivered accurately and continuously to the designated equipment or reactor as needed.
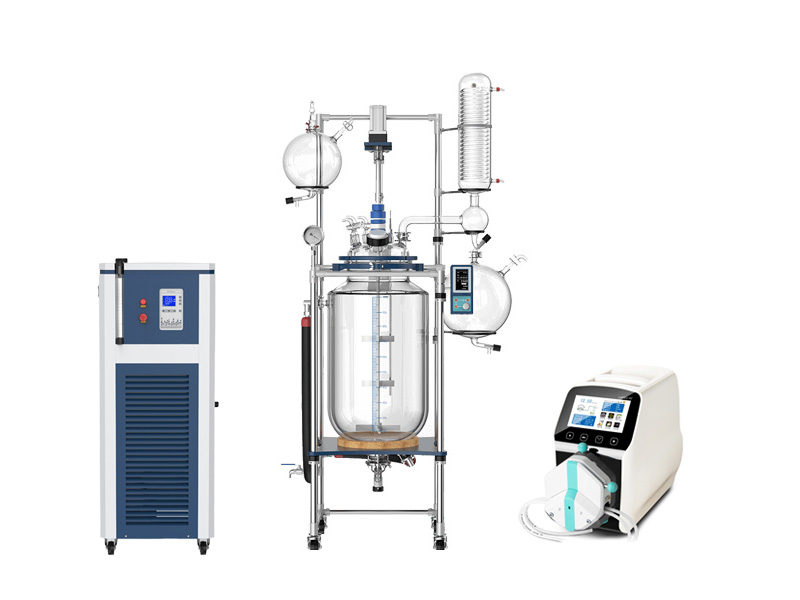
Main Functions of a Feed Pump:
Liquid Transport: Transfers liquid materials from storage containers or piping systems to production equipment, reactors, filtration systems, etc.
Flow Control: By adjusting the pump’s operating parameters, the flow rate of the liquid can be precisely controlled to meet process requirements.
Pressure Boosting: Some feed pumps can increase the pressure of the liquid to ensure it is delivered to the target location under high-pressure conditions.
How to Choose a Laboratory Glass Reactor Feed Pump:
Types of Feed Pumps Commonly Used for Laboratory Glass Reactors:
Peristaltic Pump:
Advantages: The medium only contacts the hose, reducing the risk of contamination and cross-contamination; flow is precisely controllable, making it suitable for transporting corrosive liquids, suspensions, or liquids with particles.
Applications: Due to its easy cleaning and simple operation, it is commonly used for transporting solvents, acids, bases, and other sensitive liquids, making it very suitable for laboratory environments.
Diaphragm Pump:
Advantages: Can handle corrosive or volatile liquids, with excellent leak-proof performance, suitable for applications requiring high sealing.
Applications: Commonly used for transporting corrosive chemicals, liquids containing particles, or other liquids where leakage must be avoided.
Gear Pump:
Advantages: Suitable for transporting high-viscosity liquids, with high precision delivery capability; compact structure and strong durability.
Applications: Used for precise metering of viscous chemicals, resins, or oils in reactions.
Syringe Pump:
Advantages: Extremely precise flow, suitable for small volume and high-precision liquid delivery; easy to control the delivery speed.
Applications: Particularly useful for trace addition and titration processes, commonly found in experiments requiring precise control of reaction feed rates, such as in pharmaceuticals and chemical synthesis.
Magnetic Drive Pump:
Advantages: No mechanical seals, eliminating the risk of leakage; suitable for corrosive and volatile chemicals.
Applications: Often used for transporting acids, bases, and other liquids requiring sealed protection, ensuring safety and purity in laboratory operations.
When selecting a feed pump, you need to consider the following factors:
Chemical Compatibility: Ensure that the pump materials can withstand the chemicals being transported.
Flow and Pressure Requirements: Choose a pump that meets the reactor’s demands.
Ease of Operation: Laboratory pumps should be easy to use, clean, and maintain.
Precision and Control: The accuracy of the pump is crucial for processes that require precise control of feed rates.
In summary, peristaltic pumps and syringe pumps are most commonly used in laboratory glass reactors due to their high precision, strong controllability, and ability to handle various types of chemical media.
If your experiment requires long-term continuous liquid delivery, we recommend using a peristaltic pump; if the experiment demands extremely high precision with lower flow rates, a syringe pump would be more suitable.
Peristaltic Pump Image:
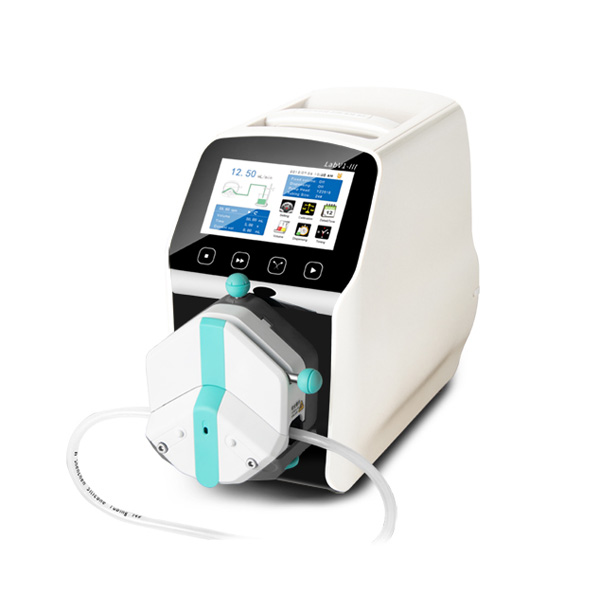