Table of Contents
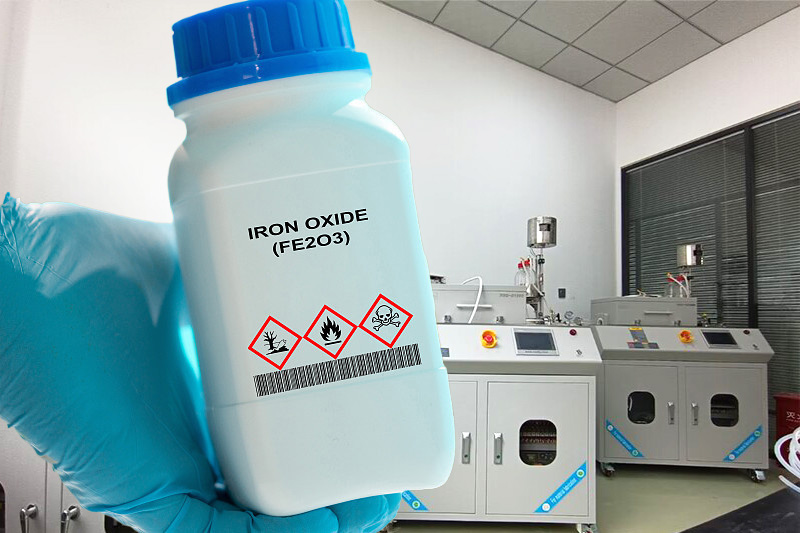
What is Hydrogen Reduction of Metal Oxides?
Hydrogen reduction of metal oxides is a process that converts metal oxides into pure metals through a chemical reaction. In this process, hydrogen gas acts as the reducing agent, reacting with the oxygen in the metal oxides to produce water vapor and leave behind the metal.
This process is carried out under high-temperature conditions and is commonly used to produce pure metal powders or for further metallurgical processing.
Basic Principle:
The core reaction of hydrogen reduction is the reaction between metal oxides (MxOy) and hydrogen gas (H₂), producing metal (M) and water vapor (H₂O). The general chemical reaction equation is:
MxOy+yH₂→xM+yH₂O
For example, the hydrogen reduction reaction of tungsten oxide (WO₃) is:
WO3+3H2=W+3H2O
Since tungsten has four relatively stable oxides, the reduction reaction actually proceeds in the following sequence:
WO3+0.1H2=WO2.90+0.1H2O
WO2.90+0.18H2=WO2.72+0.18H2O
WO2.72+0.72H2=WO2+0.72H2O
WO2+2H2=W+2H2O
The phase transition process under different reduction conditions can be illustrated as shown in the diagram:
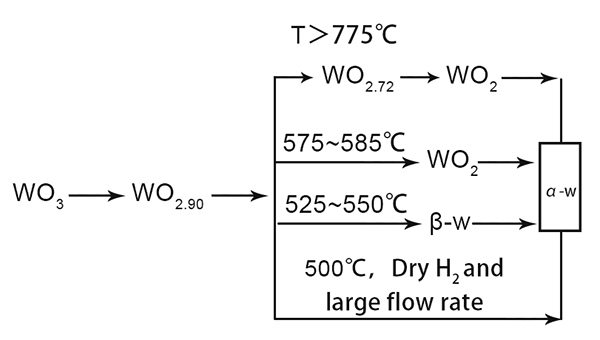
Process of Hydrogen Reduction of Metal Oxides:
The hydrogen reduction method for producing metal powders is characterized by high purity, stability, reliability, low cost, and environmental friendliness.
The main process steps are: Metal Oxide → Hydrogen Reduction → Sieving → Quality Testing → Metal Powder.
During the reduction process, various parameters such as reduction temperature, bed thickness, hydrogen flow rate, and hydrogen flow direction can be adjusted to control the particle size of the metal powder obtained.
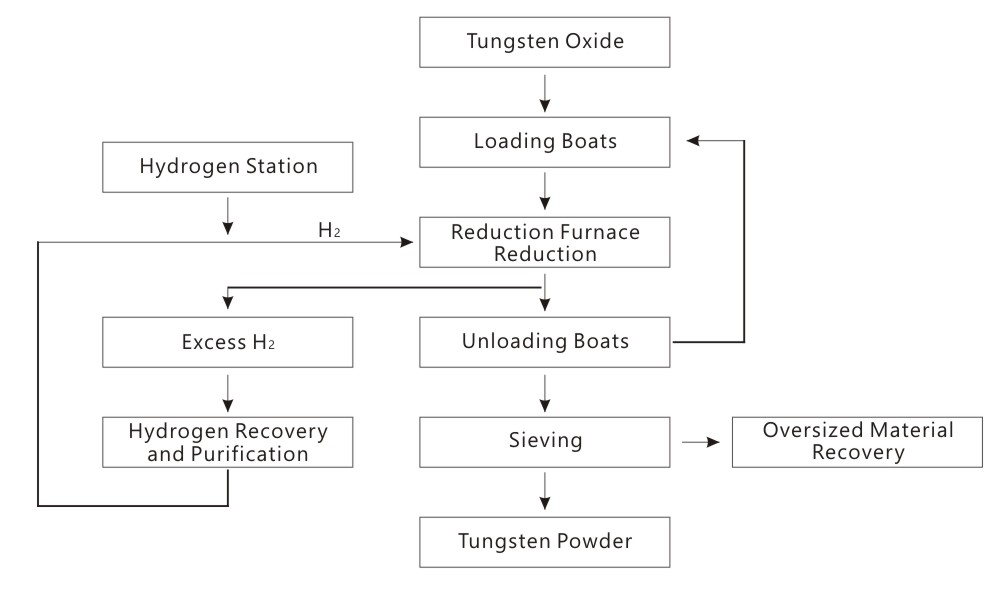
Applications:
Metal Powder Production
- Hard Alloys: Production of tungsten powder, molybdenum powder, etc., used for manufacturing hard alloy materials, widely applied in cutting tools, drill bits, and wear-resistant components.
- Electronic Materials: Preparation of high-purity metal powders (e.g., tungsten, molybdenum) used in electronic devices such as filaments, electron tubes, and emitters.
Metallurgical Industry
- Metal Extraction: Extraction of metals such as iron, molybdenum, and tungsten from ores or concentrates for further metallurgical processing.
- Alloy Manufacturing: Metal powders produced by hydrogen reduction can be used as alloy additives to improve the performance and characteristics of alloys.
High-Tech Materials
- Catalysts: Preparation of high-purity metal catalysts used in chemical reactions as catalysts and catalyst carriers.
- New Energy Materials: Used in the production of high-performance metal materials and alloys in new energy technologies such as lithium batteries and fuel cells.
Advanced Manufacturing Technologies
- Additive Manufacturing: Use of hydrogen-reduced metal powders as raw materials for additive manufacturing (3D printing) to produce complex metal parts and structures.
- Powder Metallurgy: In the powder metallurgy process, hydrogen reduction is used to prepare powders, which are then used for sintering, forming, and processing high-performance metal components.
Aerospace
- High-Temperature Alloys: Used in high-temperature alloy materials in the aerospace industry to meet performance requirements in extreme environments, such as jet engines and missile components.
Key Equipment:
Reduction Furnace
The reduction furnace is the core equipment in the hydrogen reduction process of metal oxides, providing a high-temperature environment and stable gas flow to facilitate the reduction reaction of metal oxides.
Mini Hydrogen Reduction Furnace
This mini hydrogen reduction furnace is compact and highly suitable for small-scale hydrogen reduction research in laboratories.
It features safety functions such as pressure monitoring within the furnace tube, and offers capabilities like gas shutoff and cooling. Additionally, it can ignite and handle combustible exhaust gases and is equipped with a dual ignition protection system to ensure complete combustion of the emitted gases. When used in conjunction with a tube furnace, it can also automatically clean and replace the gas within the furnace tube to achieve optimal performance.
Large Caliber Hydrogen Reduction Furnace
The large-diameter hydrogen reduction furnace is suitable for sample preparation of various materials under a clean environment with a reducing atmosphere.
The product features annularly distributed heating, providing uniform heating. The heating elements are located outside the high-purity quartz vacuum chamber, resulting in high thermal efficiency, rapid heating, and excellent temperature uniformity. The protective atmosphere circulates evenly within the furnace, ensuring uniform inflow and outflow for optimal performance.
Intelligent Sliding Hydrogen Atmosphere Furnace
The intelligent sliding hydrogen atmosphere furnace is composed of a sliding furnace chamber, a stainless steel quick-release reaction chamber, a liquid-gas supply system, a high-vacuum molecular pump set, and a gas safety protection system.
The control system utilizes an advanced PLC combined with a touchscreen operating system. The system is pre-programmed with five automatic sintering modes: dry hydrogen sintering, wet hydrogen sintering, low-vacuum sintering, high-vacuum sintering, and protective atmosphere sintering. These modes can be selected based on process requirements. The entire experiment process is fully automated, with the furnace chamber automatically sliding away after sintering (to achieve rapid material cooling). Once the set temperature is reached, the gas supply automatically shuts off, completing the entire experiment process.
Intelligent Experimental Hydrogen Reduction Furnace
The intelligent experimental hydrogen reduction furnace is suitable for various applications in industries such as metal heat treatment under reducing atmospheres, rare earth preparation, electronic lighting, crystal annealing, special alloys, magnetic materials, and precision casting. It is used for processes such as vacuum sintering, atmosphere-controlled sintering, reduction sintering, CVD experiments, and material composition measurement.
1200°C/1500°C Hydrogen Reduction Sintering Furnace
The Hydrogen Reduction Sintering Furnace is a specialized equipment developed for higher education institutions, research institutes, and industrial enterprises. It is designed for sintering, melting, and analyzing metals, non-metals, and other compound materials under atmospheric and vacuum conditions.
Gas Control System
The gas control system is a key component that ensures the reduction process is conducted safely, efficiently, and accurately. This system is primarily responsible for hydrogen supply, flow control, gas purification, and exhaust management.