Table of Contents
Hydrogen reduction furnaces are specialized thermal processing equipment designed to carry out reduction reactions in a hydrogen atmosphere. These furnaces play a critical role in various industries, particularly in the field of material science, metallurgy, and advanced manufacturing. In this blog, we’ll explore what a hydrogen reduction furnace is, its key applications, and why it’s a crucial tool in modern material processing.
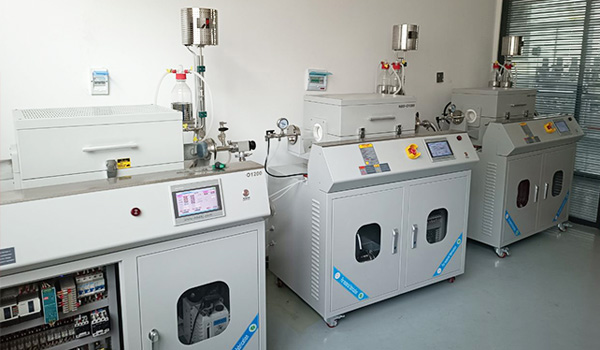
What is a Hydrogen Reduction Furnace?
A hydrogen reduction furnace is a type of industrial furnace used to reduce metal oxides or other compounds into their pure metallic state by removing oxygen.
This is achieved by heating the material in a controlled atmosphere, typically composed of hydrogen gas, which serves as the reducing agent. The furnace’s environment is meticulously controlled to prevent oxidation and ensure that the reduction process occurs efficiently.
How Does It Work?
The core process in a hydrogen reduction furnace is the chemical reaction between hydrogen and metal oxides. This can be represented by the following general reaction:
MO+H2→M+H2O
Where:
• MO represents the metal oxide
• H₂ is the hydrogen gas
• M is the pure metal
• H₂O is the water vapor formed as a byproduct
The key components of a hydrogen reduction furnace include:
Heating Chamber: The zone where the material is heated to the required temperature.
Cooling Zone: After the reduction process, the material is gradually cooled in a controlled environment to prevent oxidation.
Gas Exhaust System: Safely removes the water vapor and any excess hydrogen gas from the furnace.
Applications of Hydrogen Reduction Furnaces
Hydrogen reduction furnaces are used in a wide range of applications, particularly in industries that require high-purity metals and advanced materials. Some of the key applications include:
Metal Refining:
Hydrogen reduction is often used to produce high-purity metals such as tungsten, molybdenum, and cobalt. These metals are essential in various high-tech applications, including electronics, aerospace, and medical devices.
Powder Metallurgy:
In the production of metal powders, hydrogen reduction furnaces are used to reduce metal oxides to their pure metallic forms. These powders are then used in the manufacturing of components through techniques like additive manufacturing and sintering.
Advanced Ceramics:
Certain ceramics require the reduction of metal oxides to achieve specific properties. Hydrogen reduction furnaces are utilized to process these ceramics, making them suitable for high-temperature applications and electronic devices.
Hydrogen Storage Materials:
With the growing interest in hydrogen as a clean energy source, hydrogen reduction furnaces are used to develop and refine materials that can efficiently store hydrogen, such as metal hydrides.
Advantages of Hydrogen Reduction Furnaces
Hydrogen reduction furnaces offer several advantages over other reduction methods:
High Purity Output: The use of hydrogen gas ensures minimal contamination, producing metals of high purity.
Controlled Atmosphere: The furnace provides a controlled environment, essential for reducing sensitive materials without oxidation.
Efficiency: Hydrogen is a highly effective reducing agent, leading to quicker reaction times and lower energy consumption.
Versatility: Suitable for reducing a wide range of metal oxides, making it a versatile tool in material processing.
Hydrogen Reduction Furnace Style
Safety Considerations
While hydrogen reduction furnaces are highly effective, they also require careful handling due to the use of hydrogen gas, which is highly flammable. Key safety measures include:
Proper Ventilation: Ensuring adequate ventilation to prevent hydrogen accumulation.
Leak Detection: Regular monitoring for hydrogen leaks using specialized sensors.
Temperature Control: Maintaining precise control over furnace temperatures to prevent overheating.
Training: Ensuring operators are well-trained in handling hydrogen and operating the furnace safely.
Hydrogen reduction furnaces are indispensable tools in the modern manufacturing landscape. Their ability to produce high-purity metals and materials with precise properties makes them essential in various advanced industries.
As technology continues to evolve, the role of hydrogen reduction furnaces will only become more critical, driving innovations in material science and sustainable manufacturing.
Whether you are involved in metal refining, powder metallurgy, or advanced ceramics, understanding the capabilities and applications of hydrogen reduction furnaces can help you optimize your processes and achieve superior results.