Table of Contents
Biochar is a high-carbon, porous solid material produced by pyrolyzing biomass under oxygen-limited or inert gas conditions.
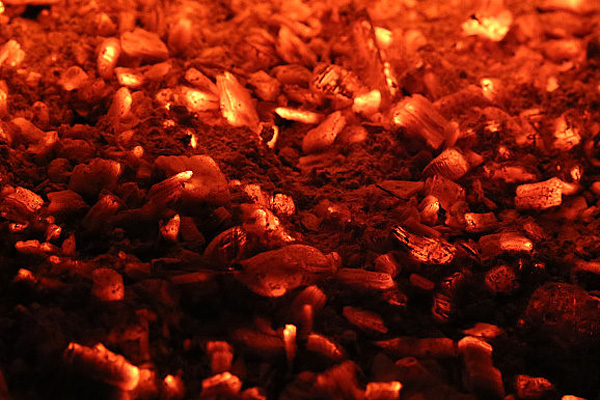
In laboratories, a muffle furnace is commonly used for biochar preparation, as it provides a stable high-temperature environment to ensure process control.
This article will detail the use of a muffle furnace for biochar production and discuss key factors affecting biochar quality.
Basic Principles of Biochar Production
The preparation of biochar primarily involves pyrolysis, where biomass is heated in an oxygen-deficient or inert gas (such as nitrogen or argon) environment. This process decomposes the biomass, releasing volatile compounds and leaving behind a carbonaceous solid.
Key Pyrolysis Parameters:
- Pyrolysis Temperature: Typically between 300–800°C, influencing biochar’s carbon content, porosity, and adsorption properties.
- Heating Rate: Usually 5–20°C/min, affecting biochar’s structural stability.
- Retention Time: Generally 30–120 minutes, impacting carbon retention and volatile matter content.
- Atmosphere Control: Using nitrogen or CO₂ minimizes oxidation, enhancing carbonization efficiency.
Material Preparation
1. Selection of Raw Materials
The properties of biochar depend on the type of raw materials used, as different biomasses vary in carbon content, ash content, and porosity:
Raw Material | Carbon Content (%) | Ash Content (%) | Application |
Hardwood (Oak, Pine) | 75–85 | 1–5 | Soil improvement, water treatment |
Crop Residues (Rice Husk, Wheat Straw) | 60–75 | 10–20 | Organic fertilizers, carbon sequestration |
Animal Manure (Chicken, Cow) | 45–60 | 20–30 | Soil nutrient enhancement |
Bamboo | 70–80 | 5–10 | Air purification, heavy metal adsorption |
Raw materials should be clean, impurity-free, and dried to a moisture content below 10%, either by air drying or low-temperature drying at 60°C for 24 hours.
2. Required Equipment and Tools
- Muffle Furnace (Temperature Range: Room Temperature – 1200°C)
- Crucible or High-Temperature Ceramic Boat (for holding biomass)
- Atmosphere Control System (optional, provides nitrogen/CO₂ flow)
- Electronic Balance (for weighing raw materials and final biochar yield)
- Gloves and Safety Glasses (for protection)
Step-by-Step Procedure
1. Loading Biomass
- Cut/Grind Raw Materials: Particle size is typically 1–5 mm to increase surface area and improve carbonization uniformity.
- Load into Ceramic Boat: Avoid excessive stacking; a layer thickness of ≤2 cm ensures even pyrolysis.
- Weigh and Record Initial Mass (M₀) for yield calculation.
2. Setting Muffle Furnace Parameters
The properties of biochar change at different temperatures:
Temperature (°C) | Carbon Content (%) | Surface Area (m²/g) | pH Value | Recommended Application |
300 | 50–60 | 10–50 | 5–6 | Soil improvement |
500 | 70–80 | 100–300 | 7–8 | Water treatment, adsorbents |
700 | 85–90 | 400–800 | 9–10 | Carbon sequestration, catalysts |
Recommended Settings:
- Heating Rate: 10°C/min
- Final Temperature: 500–600°C
- Holding Time: 1–2 hours
This setup yields biochar with a high surface area and stable carbon content.
3. Cooling and Collection
- Natural Cooling: After the holding period, turn off the muffle furnace and allow the sample to cool inside the furnace to room temperature to avoid oxidation.
- Weigh Final Biochar (M₁) and calculate carbonization yield.
Typical biochar yield ranges 30–50%, depending on the raw material and pyrolysis temperature.
Factors Affecting Biochar Quality
1. Raw Material Type
Different biomasses have varying carbon content, which affects yield and porosity:
- Wood-based biomass: High carbon content, rich in pores, suitable for adsorption.
- Crop residues: Higher ash content, ideal for soil amendments.
- Animal manure: Rich in nutrients, beneficial for organic fertilizers.
2. Pyrolysis Temperature
- Low Temperature (300–400°C): Fewer pores, higher volatile matter, suitable for soil applications.
- Medium Temperature (500–600°C): Increased surface area, optimal for water treatment and carbon sequestration.
- High Temperature (700–800°C): High carbon content, suitable for catalyst supports or activated carbon production.
Studies show that increasing temperature from 400°C to 700°C can enhance biochar’s surface area by over 300%.
3. Atmosphere Control
- Inert Gas (N₂, CO₂): Minimizes oxidation, increasing carbon retention.
- Air Atmosphere: Partial combustion may reduce yield.
Experimental results indicate that 500°C pyrolysis under nitrogen protection can achieve 80% carbon yield, whereas air atmosphere reduces it to 50%.
Applications of Biochar
Biochar’s porous structure, high adsorption capacity, and high carbon content make it widely applicable in:
- Soil Improvement (enhances water retention and nutrient storage).
- Water Treatment (removes heavy metals and organic pollutants).
- Carbon Sequestration (reduces atmospheric CO₂, mitigating climate change).
- Catalyst Supports (used in fuel cells and chemical catalysis).
Conclusion
Using a muffle furnace to produce biochar is an efficient and controllable method. By adjusting the temperature, atmosphere, and raw material types, biochar with different properties can be produced, making it suitable for various fields such as agriculture, environmental protection, and energy.
In the future, as research into biochar deepens, it will play an even more significant role in sustainable development and carbon neutrality goals.
For more information on ZYLAB muffle furnaces or to inquire about custom solutions, feel free to contact us.
Share this entry
You might also like