Table of Contents
Introduction
Silicon carbide (SiC) coatings are widely used in aerospace, semiconductor, nuclear, and photovoltaic industries due to their exceptional properties, such as high hardness, thermal stability, and corrosion resistance. Achieving high-quality SiC coatings requires advanced deposition technologies, and among them, High Vacuum Chemical Vapor Deposition (CVD) Furnaces stand out as a preferred solution.
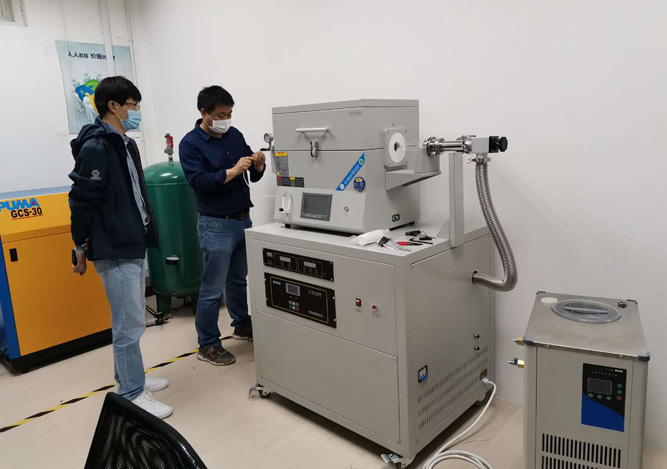
In this article, we explore how high vacuum CVD furnaces are used for SiC coating preparation and why they are crucial in modern material science.
Why Choose a High Vacuum CVD Furnace for SiC Coatings?
1. Superior Coating Purity
A high vacuum environment significantly reduces contamination from oxygen, moisture, and other impurities. This ensures that the deposited SiC layer maintains high purity and optimal chemical properties, which is essential for demanding applications such as semiconductor processing and nuclear reactors.
2. Uniform and Dense Coating
High vacuum CVD furnaces offer precise temperature and gas flow control. This capability enables the formation of uniform, dense, and defect-free SiC coatings, even on complex geometries or large workpieces.
3. Enhanced Adhesion and Mechanical Properties
The controlled deposition environment improves the adhesion between the SiC coating and the substrate. As a result, the coatings exhibit excellent wear resistance, thermal shock resistance, and mechanical strength, extending the service life of components.
Typical Applications of SiC Coatings Prepared by High Vacuum CVD Furnace
Application | Benefit |
Aerospace Components | High-temperature stability, oxidation resistance |
Nuclear Fuel Cladding | Radiation tolerance, chemical inertness |
Semiconductor Process Equipment | Protection against corrosion and particle contamination |
Optical Mirrors & IR Windows | Scratch resistance, thermal conductivity |
The CVD Process for SiC Coating Preparation
1. Substrate Preparation
The substrate material is cleaned and pre-treated to ensure proper adhesion of the SiC layer.
2. Vacuum Pumping
The CVD furnace is evacuated to a high vacuum level, typically below 10⁻³ Pa, minimizing contamination.
3. Heating Phase
The substrate is heated to the required process temperature, usually between 1000°C and 1600°C.
4. Gas Introduction and Deposition
Precursor gases such as silane (SiH₄), methane (CH₄), or methyltrichlorosilane (MTS) are introduced. Under high temperature and vacuum, these gases decompose and react to form a uniform SiC coating on the substrate.
5. Cooling and Venting
After the deposition process, the system cools down under controlled conditions before being vented to atmospheric pressure.
Advantages of ZYLAB High Vacuum CVD Furnace
1. Precise Temperature Control
Multi-zone heating elements allow for accurate temperature gradients and uniform heat distribution.
2. Efficient Gas Utilization
Integrated mass flow controllers (MFCs) ensure accurate delivery of process gases.
3. Customizable Chamber Designs
Tailored furnace chambers accommodate various substrate sizes, from small components to large workpieces.
4. Automated Process Control
PLC-based systems and touchscreen interfaces offer user-friendly operation and process monitoring.
Conclusion
High vacuum CVD furnaces are essential for producing high-performance silicon carbide (SiC) coatings. Whether for aerospace, semiconductor, or nuclear applications, these systems ensure exceptional purity, precision, and consistent quality to meet the demands of advanced industries.
If your project requires reliable and high-quality SiC coating solutions, a high vacuum CVD furnace is the ideal choice.
ZYLAB offers advanced high vacuum CVD furnaces designed for both research and industrial production. Contact us today to explore customized solutions tailored to your specific application needs!
Share this entry
You might also like