Table of Contents
Introduction
What is a Crucible Furnace?
A crucible furnace is a type of furnace specifically designed for heating materials within a crucible. A crucible is a container made of refractory material, such as ceramic or graphite, that can withstand high temperatures. Crucible furnaces are commonly used in laboratories and industrial settings for various heating processes, such as melting, calcination, and heat treatment of materials.
These furnaces typically consist of a chamber where the crucible is placed, heating elements that provide the necessary heat, temperature control mechanisms, and insulation to maintain high temperatures. They are available in different sizes and configurations depending on the specific application requirements.
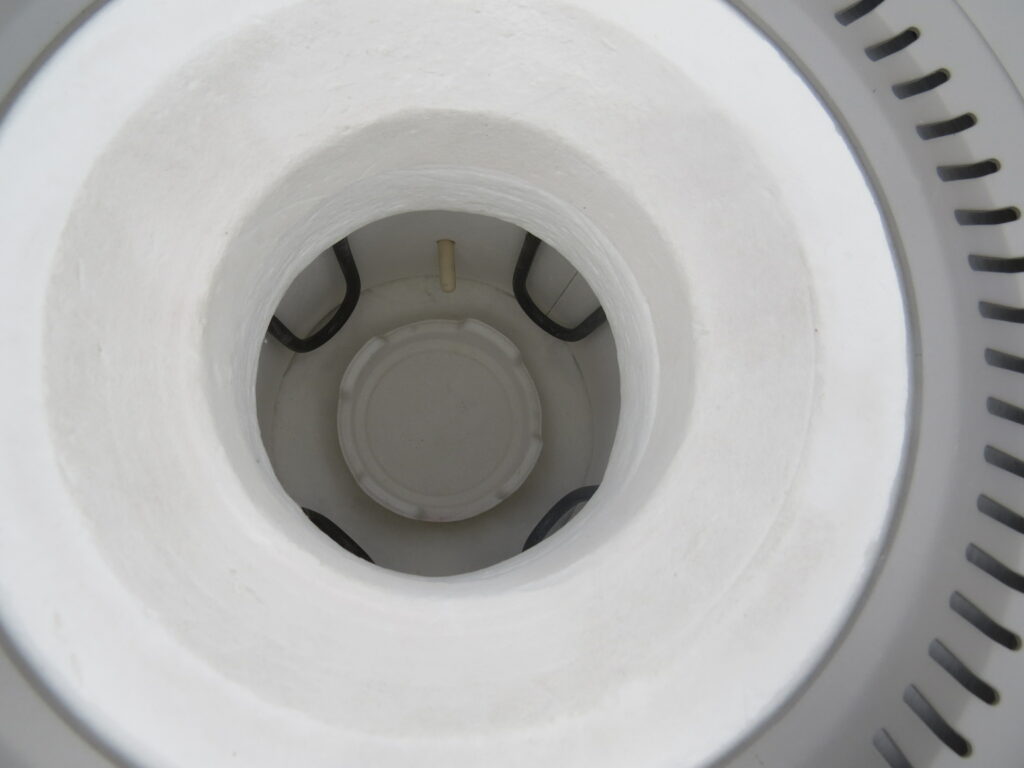
Crucible furnaces are versatile and can accommodate a wide range of materials, making them useful in various fields including metallurgy, ceramics, glass manufacturing, and materials science research. They are often preferred for their ability to provide precise temperature control and uniform heating, making them essential equipment for many thermal processing applications.
Here are some key points about crucible furnaces:
Temperature Control: They offer precise temperature control to meet specific heating requirements, allowing for uniform heating of materials.
Size and Configuration: Crucible furnaces come in different sizes and configurations to suit different applications and heating capacities.
Heating Elements: They typically feature heating elements, such as resistive coils, SiC or MoSi2 ,etc, to provide the necessary heat for the process.
Insulation: They are equipped with insulation materials to maintain high temperatures and improve energy efficiency.
Safety Features: Crucible furnaces may include safety features such as temperature sensors, overheat protection, and safety interlocks to ensure safe operation.
Maintenance: Regular maintenance is important to ensure optimal performance and longevity of crucible furnaces, including cleaning, inspection, and replacement of worn components.
Applications
What is a Crucible Furnace Used For?
A crucible furnace is used for various heating processes involving materials placed within a crucible. Some common uses include:
Melting Metals: Crucible furnaces are often used to melt metals and alloys for casting, forging, or other manufacturing processes in foundries and metalworking industries.
Calcination: They are utilized for calcining materials, a process that involves heating substances to high temperatures to cause chemical decomposition or to remove volatile components.
Heat Treatment: Crucible furnaces are employed for heat treating materials to change their mechanical or physical properties, such as hardness, strength, or ductility.
Ceramic Processing: In ceramic manufacturing, crucible furnaces are used for sintering, firing, or annealing ceramic materials to achieve the desired properties and shapes.
Glassworking: Crucible furnaces are used in glassworking processes for melting and refining glass compositions, as well as for shaping glass into various forms.
Laboratory Research: They are commonly found in laboratory settings for conducting experiments, synthesizing materials, and studying the thermal behavior of substances.
Metallurgical Analysis: Crucible furnaces are used in metallurgical laboratories for analyzing the composition and properties of metals through processes such as fusion, cupellation, or oxidation.
Jewelry Making: In jewelry manufacturing, crucible furnaces are used for melting precious metals like gold, silver, and platinum to create jewelry components.
Chemical Synthesis: They can be employed in chemical synthesis processes for heating and reacting chemical compounds to produce desired products.
The Application of Crucible Furnaces in Powder Metallurgy Field
Powder Sintering: Crucible furnaces are used in the field of powder metallurgy for the sintering process, which involves heating powdered metals or alloys to bond their particles together, forming dense block materials. This helps to improve the density, strength, and wear resistance of materials, commonly used in manufacturing wear-resistant parts, tools, etc.
Metal Melting: In the powder metallurgy process, crucible furnaces are utilized to melt metal powders or alloy powders to their melting temperatures, for the purpose of preparing billets or for casting. This is significant for producing parts with complex shapes, alloy materials, etc.
Alloy Preparation: Crucible furnaces are also employed in alloy preparation, where different metals or elemental powders are mixed and heated to melt and mix uniformly, thereby preparing alloy materials with specific properties.
Heat Treatment Processes: In powder metallurgy processes, crucible furnaces are used for heat treatment processes of metal parts, such as annealing, quenching, normalizing, etc., to adjust the structure and properties of materials, improving their strength, hardness, etc.
Powder Fusion Welding: Crucible furnaces can also be used for powder fusion welding processes, where metal powders are heated to their molten state in the crucible, then fused with the surface of workpieces, achieving the joining and repair of metal parts.
Powder Synthesis: The powder synthesis of some special materials can also be carried out in crucible furnaces, preparing materials with specific structures and properties using powder metallurgy techniques, such as high-temperature alloys, ceramic materials, etc.
The Application of Crucible Furnaces in the Semiconductor Industry
Crystal Growth: Crucible furnaces are used in the semiconductor industry for crystal growth processes, especially in the growth of single-crystal silicon. During the crystal growth process, single-crystal silicon rods are gradually crystallized from the silicon solution in the crucible under high-temperature conditions and constant temperature control, which are used for the preparation of semiconductor devices.
Doping Processes: In the manufacturing of semiconductor devices, crucible furnaces are used for doping processes, i.e., high-temperature diffusion of dopants (such as boron, phosphorus, arsenic, etc.) with silicon crystals, changing their electrical conductivity properties to form different types of electrons or holes.
Oxidation: Crucible furnaces are also used in the semiconductor manufacturing for oxidation processes, where silicon crystals are exposed to an oxygen environment, forming silicon dioxide films on their surfaces, used for the preparation of insulating layers or dielectric layers.
Annealing Treatment: Crucible furnaces are used for annealing treatment of semiconductor devices, i.e., rearranging the lattice structure of semiconductor materials under high temperature, eliminating stress and defects, and improving the performance and stability of devices.
Film Deposition: In the process of semiconductor device manufacturing, crucible furnaces are also used for film deposition, i.e., depositing a thin film material such as silicon nitride, aluminum oxide, etc., on the surface of substrates, used for the preparation of insulating layers, via filling, etc.
Packaging: Crucible furnaces are used in the packaging process of semiconductor devices for soldering, sealing, and curing packaging materials, to protect the internal structure of devices, and provide mechanical support and protection.
Additionally, crucible furnaces are widely used in various industries such as the energy sector, environmental protection industry, food processing industry, construction materials industry, and others.
Benefit
Versatility: Crucible furnaces can be used for a wide range of applications including melting, casting, heat treating, and sintering various materials such as metals, alloys, and ceramics.
Cost-effectiveness: Crucible furnaces are often more affordable compared to other types of furnaces, making them an attractive option for small-scale operations or budget-conscious users.
Compact size: These furnaces are typically compact in size, making them suitable for laboratories, small workshops, and research facilities where space may be limited.
Ease of operation: Crucible furnaces are relatively simple to operate and require minimal training, making them accessible to a wide range of users.
Customization: They can be customized to meet specific heating requirements, including temperature control, heating rate, and holding time, ensuring precise and consistent results.
Energy efficiency: Modern crucible furnaces are designed with energy-efficient features, helping to reduce energy consumption and operating costs.
Durability: High-quality materials and construction ensure the durability and longevity of crucible furnaces, providing reliable performance over extended periods of use.
Images for Crucible Furnaces
Crucible Furnace Price
The price of crucible furnaces can vary depending on factors such as their size, capacity, features, and brand. Generally, smaller crucible furnaces designed for laboratory or small-scale applications tend to be more affordable compared to larger industrial-grade furnaces.
Specific prices for crucible furnaces can range from hundreds to thousands of dollars, with laboratory-scale models typically being on the lower end of the price spectrum and larger, more advanced industrial models being on the higher end.
It’s important to consider not only the initial purchase price but also factors such as long-term operating costs, maintenance requirements, and warranty or support services offered by the manufacturer when evaluating the overall value of a crucible furnace.
For accurate pricing information, it’s recommended to contact suppliers or manufacturers directly.
What to Consider When Purchasing Crucible Furnace?
When purchasing a crucible furnace, there are several important factors to consider to ensure that you select the right equipment for your needs:
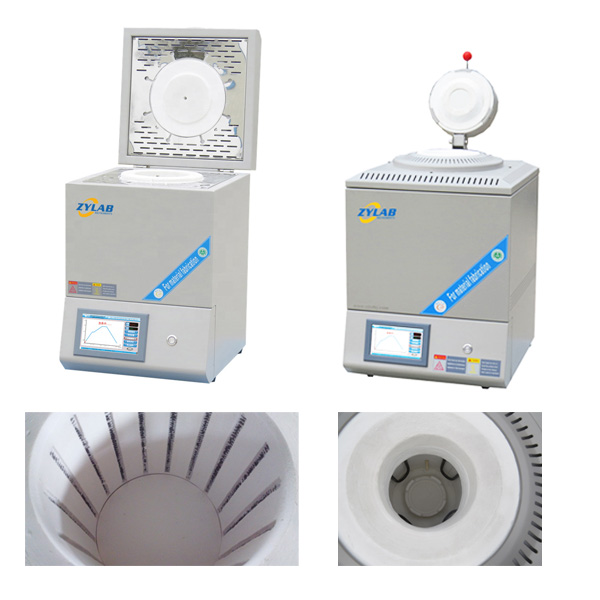
Application Requirements: Determine your specific application needs, including the types of materials you will be working with, the desired temperature range, and any special features required for your process.
Heating Capacity and Temperature Range: Consider the heating capacity and temperature range of the furnace to ensure it can reach and maintain the temperatures required for your application.
Size and Capacity: Choose a furnace size and capacity that can accommodate the volume of material you need to process without overcrowding or underutilizing the furnace chamber.
Heating Element: Evaluate the type and quality of the heating elements used in the furnace, such as resistance wire, SiC or MoSi2, to ensure they are suitable for your application and provide consistent heating.
Control System: Look for furnaces with advanced control systems that offer precise temperature control, programmable settings, and safety features to ensure reliable operation and accurate results.
Energy Efficiency: Consider the energy efficiency of the furnace to minimize operating costs and reduce environmental impact. Look for features such as insulation, thermal shielding, and energy-saving modes.
Safety Features: Choose a furnace with built-in safety features such as overtemperature protection, safety interlocks, and emergency shut-off systems to prevent accidents and ensure operator safety.
Ease of Use and Maintenance: Select a furnace that is user-friendly and easy to operate, with intuitive controls and minimal maintenance requirements. Consider factors such as ease of cleaning, access to components, and availability of spare parts.
Manufacturer Reputation and Support: Research the reputation of the furnace manufacturer, including their track record for quality, reliability, and customer support. Choose a reputable manufacturer that offers comprehensive technical support, warranty coverage, and responsive customer service.
Budget: Determine your budget and compare the features and specifications of different furnaces within your price range to find the best value for your investment.