Table of Contents
Introduction:
Cleaning inside a reaction vessel refers to the process of cleaning reactors used for chemical reactions, mixing, heating, cooling, or other process operations to remove residues, contaminants, or other impurities.
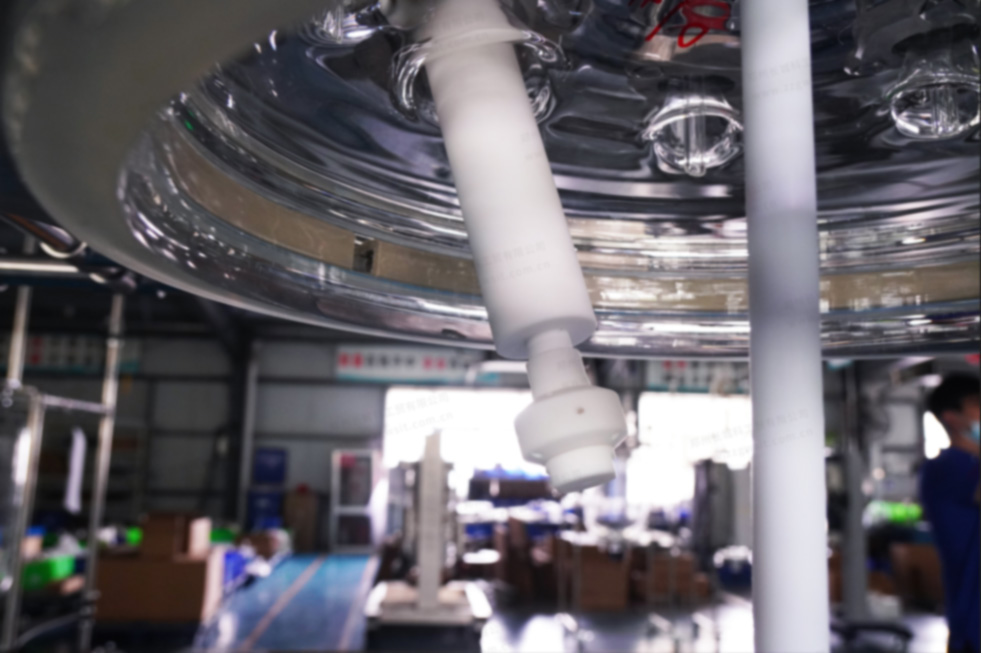
Why Use Spray Cleaning Inside the Reactor?
Protection of Glass Surface:
The interior surface of a glass reactor is relatively fragile and can be easily scratched or damaged. Spray cleaning uses liquid sprays rather than mechanical tools, effectively preventing scratches or abrasions on the glass surface, thereby extending the reactor’s lifespan.
Comprehensive Cleaning:
Spray cleaning can evenly distribute the cleaning liquid throughout all corners of the reactor via nozzles, ensuring that the entire interior surface is covered. This is particularly important for complex shapes or areas with recesses or dead spots, where spray cleaning provides more thorough cleaning.
Fast and Efficient:
Spray cleaning uses high-pressure jets to quickly remove residues from the glass surface, offering high cleaning efficiency. When combined with appropriate cleaning agents (such as acidic or alkaline cleaners), it can effectively break down and remove chemical residues inside the reactor.
Enhanced Safety:
During the cleaning process, spray cleaning reduces direct contact between personnel and the reactor interior or cleaning liquids, minimizing the risk of exposure to harmful chemicals or mechanical injuries, and thus improving the safety of the cleaning process.
Advantages of Using PTFE Material:
Broad Chemical Compatibility:
PTFE has exceptional chemical resistance, capable of withstanding nearly all acids, bases, solvents, and other chemical substances.
Prevents Contamination and Scaling:
The surface of PTFE is extremely smooth and has excellent non-stick properties, meaning the cleaning head is less likely to accumulate contaminants or scale, thus maintaining cleanliness.
Suitable for High-Temperature Operations:
PTFE can remain stable across a wide temperature range, particularly in high-temperature environments, where it retains its physical and chemical properties.
Efficient Operation:
The low friction coefficient of PTFE allows the cleaning head to operate efficiently with low energy consumption.
High Durability:
PTFE has good mechanical strength and durability, capable of withstanding the pressure and mechanical stress during the cleaning process.
PTFE Spray Cleaning Device:
The complete system includes a cleaning nozzle, spray bar, and flange.
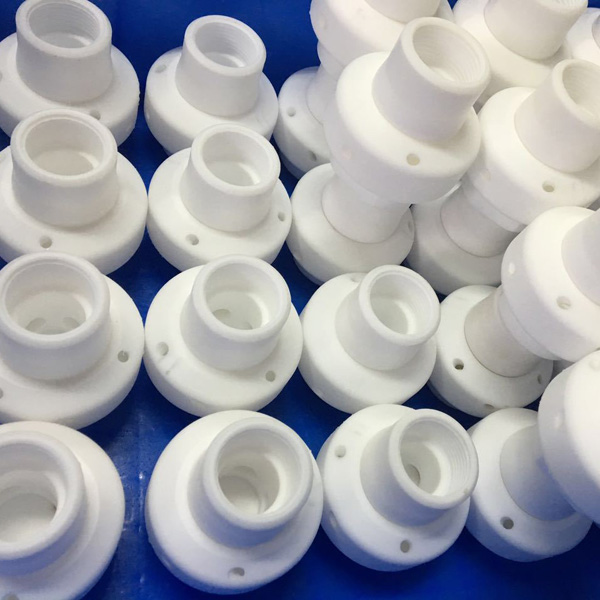
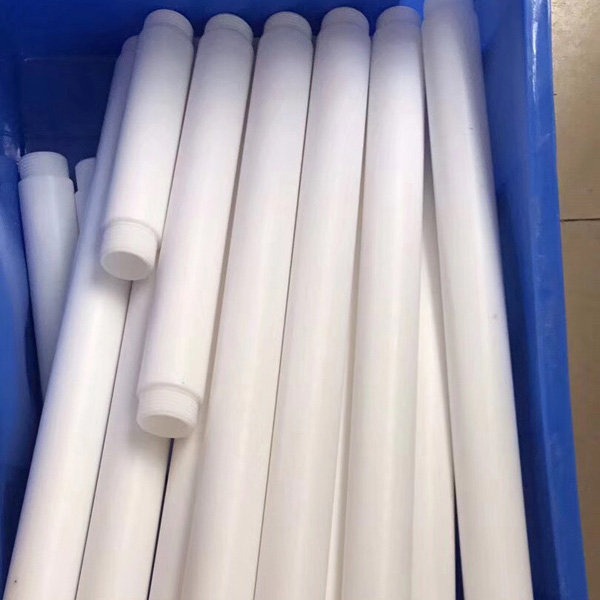
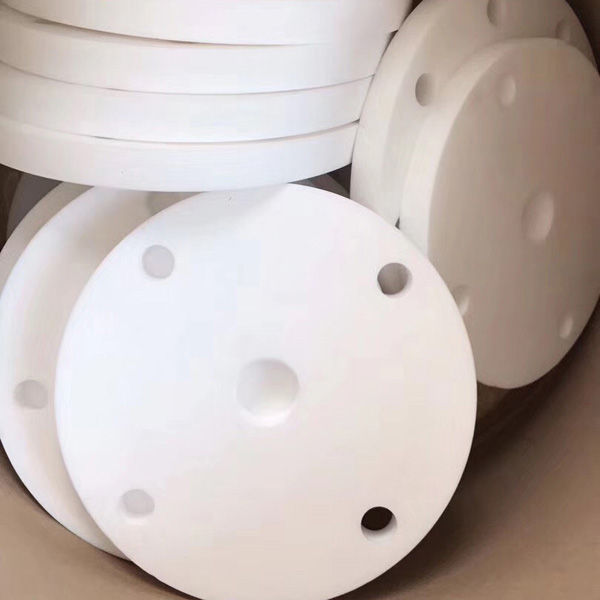
Working Principle of Rotating Cleaning Nozzle:
The rotating cleaning nozzle is driven by high-pressure water flow, which causes the internal components to rotate, allowing the nozzle to spin and spray water for comprehensive coverage. Its design continuously changes the angle and direction of the water flow, effectively removing deposits and residues from the inside of the equipment. This is particularly suitable for environments requiring corrosion resistance and hygiene.
Recommended Reaction Vessels:
Interface for Installing the Spray Cleaning Device:
Glass reaction vessels typically have 7 standard openings. The installation port for the PTFE spray cleaning device usually shares a flange with the solid feeding port, thus maintaining the 7 openings. If an additional multifunctional opening is needed, a custom vessel lid will be required.