Table of Contents
Overview of Ball Mill
The ball mill is a commonly used grinding equipment for crushing, mixing, or blending various materials, playing a crucial role in pulverizing materials after they have been crushed.
It typically consists of a rotating cylinder containing grinding balls (usually steel balls, ceramic balls, or hard alloy balls). Materials are placed inside the cylinder and ground, mixed, or blended as the cylinder rotates.
Steps in the Operation of a Ball Mill
Loading: Place the materials to be ground inside the cylinder of the ball mill.
Addition of Grinding Media: Add an appropriate amount of grinding media to the cylinder, typically steel balls, ceramic balls, or hard alloy balls. These grinding media rotate inside the cylinder with the materials and grind them.
Rotational Motion: Start the ball mill to initiate cylinder rotation. The rotation of the cylinder generates centrifugal force, causing the grinding media to be thrown against the inner wall of the cylinder, where they frictionally interact and impact with the loaded materials.
Grinding Process: The materials undergo continuous impact, compression, and friction from the grinding balls inside the cylinder, gradually being ground into fine particles or powder.
Dispersion and Mixing: During the grinding process, materials continuously mix and disperse with the grinding media, ensuring uniform grinding of the materials.
Product Collection: After grinding is complete, shut down the ball mill and remove the ground materials from the cylinder.
Selection of Grinding Jars
Material Selection: The material of the grinding jar should be chosen based on the nature and requirements of the materials to be ground. Common materials for grinding jars include stainless steel, hard alloy, ceramics, polyethylene, etc. For example, stainless steel grinding jars are typically chosen for materials prone to oxidation, while special materials may be selected for high temperature, highly corrosive, or specialized material requirements.
Capacity Selection: The capacity of the grinding jar should be selected according to the quantity of materials to be ground and the operational requirements. Generally, a larger grinding jar capacity enhances processing capabilities but also increases the size and cost of the ball mill. Choose a grinding jar with an appropriate capacity based on actual needs.
Structure and Design: The structure and design of the grinding jar should consider the operational characteristics and process requirements of the ball mill. Factors such as the shape, size, feed inlet, discharge outlet design of the grinding jar, and whether it has sealing performance, cooling or heating functions, etc., all affect the operational efficiency and product quality of the ball mill.
Wear Resistance Selection: Due to the tendency for grinding jars to experience wear during prolonged high-speed friction, the wear resistance of the grinding jar should be considered. Select a grinding jar material with good wear resistance based on the hardness and abrasiveness of the materials to be ground, in order to prolong the service life of the grinding jar.
Attachments and Additional Features: Depending on requirements, consider whether attachments and additional features such as jar covers, jar clamps, cooling systems, heating systems, etc., are needed to meet specific grinding requirements and process conditions.
Grinding Ball Grading
The grading of grinding balls in a ball mill refers to the distribution proportion of grinding balls of certain specifications and sizes added to the grinding system during the grinding process. Grinding ball grading is one of the important factors affecting the grinding effect of the ball mill, and a reasonable grading can improve grinding efficiency and product quality.
Generally, the grading of grinding balls in a ball mill should consider the following aspects:
Size Distribution of Grinding Balls: A variety of different diameters of grinding balls are usually used simultaneously inside the ball mill, ranging from larger grinding balls to smaller ones, to meet the requirements of different grinding stages. Larger grinding balls are used for primary grinding and crushing, while smaller ones are used for fine grinding and refining particle size.
Proportion of Grinding Balls: A reasonable proportion of grinding balls is crucial to ensure the grinding effect of the ball mill. Determine the proportion of different sized grinding balls based on the properties of the materials, the specifications of the ball mill, and the operating conditions, to ensure the balance and stable operation of the grinding system.
Density Distribution of Grinding Balls: The density distribution of grinding balls affects the grinding effect and uniformity of materials inside the ball mill. Controlling the density distribution of grinding balls and ensuring their uniform coverage on the surface of the cylinder can improve grinding efficiency and product quality.
Wear Resistance of Grinding Balls: Grinding balls made from different materials and manufacturing processes have different wear resistance. Considering the wear of grinding balls during prolonged high-speed friction, selecting grinding balls with good wear resistance can prolong the service life of the ball mill.
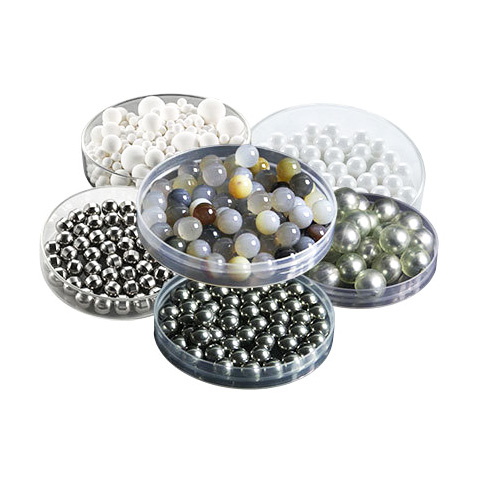
Two-Stage Ball Grading Method
The two-stage ball grading method is a method of grinding using different sizes and types of grinding balls inside the ball mill. This method employs the simultaneous use of two or more different sizes of grinding balls inside the ball mill to achieve more effective grinding and a more uniform distribution of ground materials.
Specifically, the two-stage ball grading method typically includes the following steps:
Selection of Grinding Balls: Select appropriate sizes and materials of grinding balls based on the properties and grinding requirements of the materials to be ground. Typically, larger and smaller grinding balls are chosen to cover different grinding stages and requirements.
Two-Stage Ball Grading: Mix the selected two or more different sizes of grinding balls in certain proportions and blend them as needed to ensure uniform distribution of the grinding balls.
Loading and Grinding: Add the mixed grinding balls into the grinding system of the ball mill and start the mill for grinding. During the grinding process, the two different sizes of grinding balls work together on the materials to achieve grinding effects of different particle sizes.
Applications of Ball Mills in Laboratory and Research Fields
Materials Science and Engineering: Laboratory ball mills are used for studying the properties of various materials and preparing new materials, such as metals, ceramics, and polymers.
Chemistry and Biochemistry: Used for grinding and mixing chemical reagents, preparing and analyzing biological samples, such as pharmaceutical preparation, dispersion of biological samples, and cell grinding.
Pharmaceuticals and Pharmaceutical Industry: Used for grinding and mixing pharmaceutical raw materials, preparing and testing drug formulations, and researching drug delivery systems.
Food Science and Engineering: Used for grinding and mixing food raw materials, preparing food additives, and researching food quality and safety.
Environmental Science and Engineering: Used for grinding and preparing environmental samples, preparing and testing wastewater treatment agents, and processing and utilizing solid waste.
Geology and Mineralogy: Used for grinding and preparing ore, rock, and soil samples, and analyzing and testing geological samples.
Nanoscience and Nanotechnology: Laboratory ball mills play an important role in the preparation and research of nanomaterials, such as preparing and controlling the size of nanoparticles and their characterization.
Energy Science and Technology: Used for grinding and preparing energy materials, such as battery materials, energy storage materials, and catalysts.
Overall, ball mills play an important role in various scientific research, engineering technology, and laboratory applications, providing strong technical support for material research, new material development, and scientific exploration.
The following is a laboratory ball mill provided by ZYLAB for your reference: