Table of Contents
What is a Baffled Glass Lined Reactor?
A baffled glass lined reactor is a type of chemical reaction equipment designed with multiple baffles installed on the inner wall of the reactor.
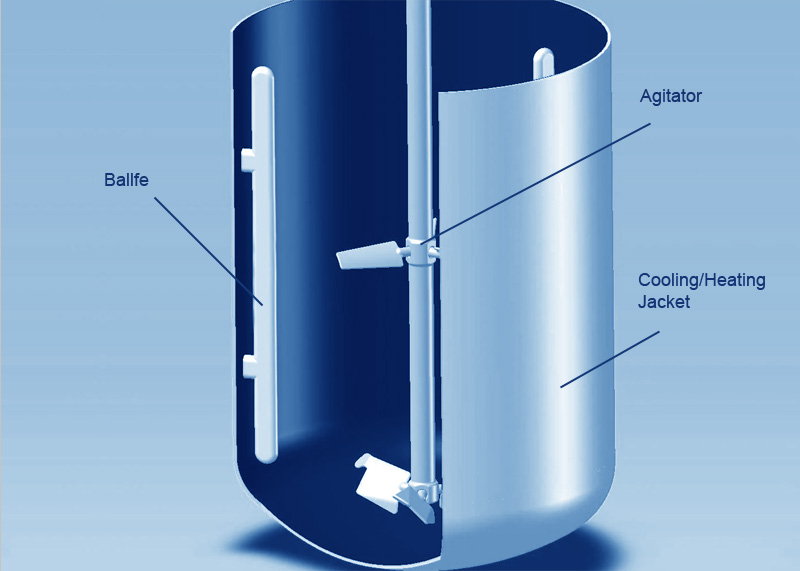
Baffles in a glass-lined reactor are fixed structures mounted on the inner wall of the reactor to improve the internal fluid dynamics, enhancing stirring and mixing efficiency.
They are typically vertical or slightly inclined elongated structures arranged close to the inner wall of the reactor.
Functions of Baffles:
Preventing Vortex Formation:
Without baffles, the agitator can cause the liquid to form a rotating vortex. This vortex leads to uneven fluid flow within the reactor, resulting in poor mixing. Baffles disrupt this rotational flow, preventing vortex formation and ensuring uniform distribution of liquid within the reactor.
Enhancing Mixing Efficiency:
Baffles increase the degree of turbulence in the liquid, allowing reactants to mix more uniformly. This is crucial for ensuring the uniformity and consistency of chemical reactions, especially in cases involving complex reactions.
Improving Solid Suspension:
In reactions involving solid particles, baffles help keep the particles evenly suspended, preventing them from settling at the bottom of the reactor. This is particularly important for processes where solid-liquid contact is essential.
Promoting Heat Transfer:
By enhancing fluid flow, baffles promote heat transfer within the reactor, ensuring more uniform heating or cooling. This helps maintain temperature balance within the reactor, thereby improving reaction efficiency.
Optimizing Reaction Speed:
By improving mixing and heat transfer efficiency, baffles can accelerate the contact and reaction rate of reactants, thus increasing the overall reaction speed and yield.
Does your glass-lined reactor need baffles?
If your glass vessel is square or rectangular, the geometric shape of the container walls eliminates the need for baffles.
However, most glass vessels are cylindrical. Without a baffle system, the reactor’s stirring motor will create a vortex after about one minute of operation, leading to an ineffective mixing environment.
If the reactor has heating or cooling coils, these coils can, to some extent, substitute for baffles, eliminating the need for additional baffles.
Types of Baffles:
Fixed Baffles:
A type of baffle that is permanently fixed to the inner wall of the reactor and is not removable. It usually requires no maintenance or adjustment, making it suitable for experimental environments that need stable, long-term operation.
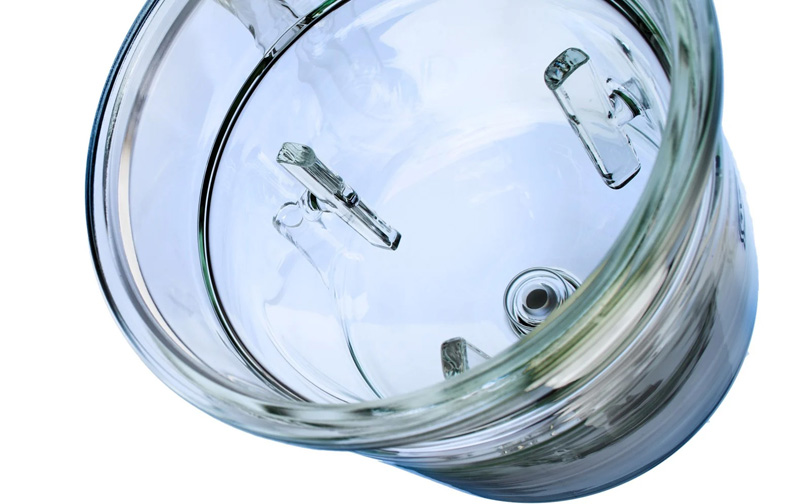
Its design is simple, integrated with the reactor, with no complex structural components, making it easy to clean and maintain.
Insertable Baffles:
Highly flexible, allowing experimenters to choose whether to use the baffles based on specific mixing requirements. They are easy to install and remove, facilitating reactor cleaning and maintenance.
Baffle Materials:
Our reactors are typically made from high-quality borosilicate glass, so the material for fixed baffles is consistent with the reactor, using high-quality borosilicate glass.
This material offers excellent chemical stability, heat resistance, and mechanical strength, making it widely used in fields such as chemical engineering, pharmaceuticals, food processing, and materials science.
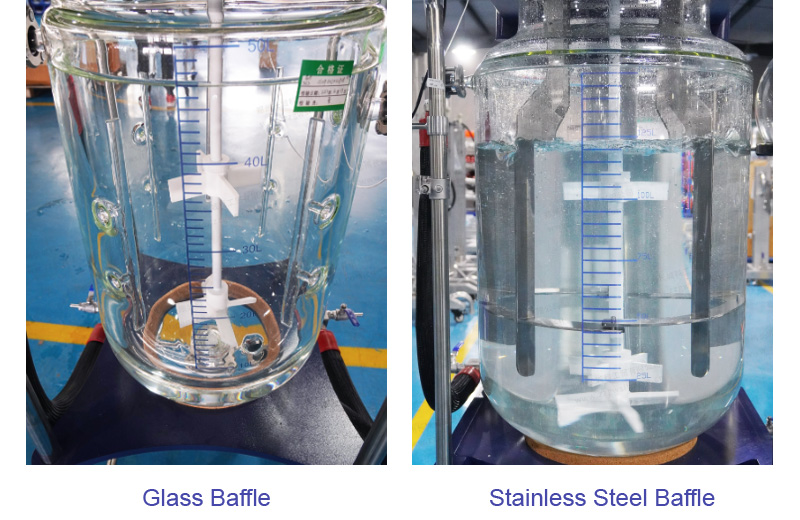
Insertable baffles are generally made from stainless steel and PTFE-coated materials.
Stainless steel baffles are widely used in chemical engineering, pharmaceuticals, and food processing due to their mechanical strength, durability, and good resistance to neutral chemicals.
PTFE-coated baffles, with their outstanding chemical resistance, low friction coefficient, and anti-adhesion properties, are suitable for applications involving highly corrosive chemicals and environments requiring high purity.
Baffle Dimensions:
The length of the baffles is typically proportional to the height of the reactor. Generally, the length of the baffles is about one-third to two-thirds of the height of the reactor to ensure they effectively disrupt vortex formation.
The width of the baffles is usually between 1/12 to 1/10 of the reactor’s diameter, to avoid occupying too much internal space while maintaining good stirring performance.
Common Baffle Configurations for Glass-Lined Reactors:
For very small reactors used in experiments or for stirring low-viscosity liquids, 2 baffles are generally sufficient.
The most common configuration is 4 baffles, which is suitable for most cylindrical reactors and provides good mixing performance.
For large reactors or complex mixing processes, we recommend installing 6 baffles to ensure more uniform and effective stirring.