Table of Contents
Overview
Aerosol-Assisted Chemical Vapor Deposition (AACVD) is a specialized technique used for the deposition of thin films and coatings on various substrates.
Unlike traditional Chemical Vapor Deposition (CVD), which relies solely on gaseous precursors, AACVD utilizes aerosols—finely dispersed droplets of a precursor solution suspended in a carrier gas—to transport the precursor materials to the deposition zone.
How AACVD System Works
Precursor Preparation:
A solution containing the desired precursor materials is prepared. This solution can include metal-organic compounds, inorganic salts, or other chemical precursors dissolved in a suitable solvent.
Aerosol Generation:
The precursor solution is atomized to form fine droplets (aerosols) using an ultrasonic or pneumatic nebulizer. These aerosols are then carried by a flow of gas, typically nitrogen or argon, into the reaction chamber.
Deposition Process:
The aerosol is transported to a heated substrate within the reaction chamber. Upon reaching the hot surface, the solvent evaporates, and the precursor undergoes a chemical reaction, leading to the formation of a solid film or coating on the substrate.
Film Formation:
The resulting film can be composed of various materials, including oxides, nitrides, metals, or polymers, depending on the precursor used. The thickness, composition, and morphology of the film can be precisely controlled by adjusting parameters such as temperature, gas flow rate, and precursor concentration.
Key Features of AACVD System
Versatility:
AACVD is suitable for a wide range of materials, including complex oxides, metals, and composite films. It can be used to deposit coatings on various substrates like glass, metals, ceramics, and polymers.
Scalability:
The AACVD process can be scaled from laboratory research to industrial production, making it a flexible option for both small-scale experiments and large-scale manufacturing.
Controlled Deposition:
AACVD allows for precise control over film properties such as thickness, uniformity, and morphology. By fine-tuning the process parameters, films with specific characteristics can be produced.
Low Cost:
Compared to conventional CVD, AACVD can be more cost-effective, as it often uses liquid precursors that are easier to handle and less expensive than gaseous ones.
Applications
Electronics:
Thin Film Transistors (TFTs): Used in the fabrication of active layers in TFTs for displays.
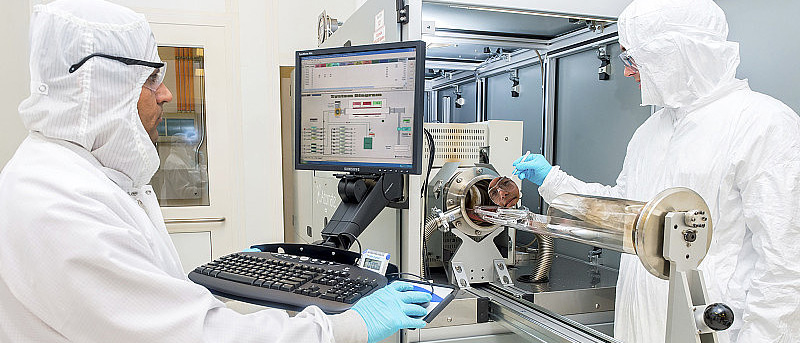
Transparent Conductive Oxides (TCOs): Deposits materials like indium tin oxide (ITO) used in touch screens and solar cells.
Energy:
Solar Cells: AACVD is used to deposit photovoltaic materials like perovskites and cadmium telluride (CdTe).
Battery Materials: Used in the deposition of thin films for battery electrodes, enhancing energy storage capacity.
Optics:
Anti-Reflective Coatings: Deposits coatings that reduce reflection on lenses and other optical components.
Waveguides: Fabrication of optical waveguides used in photonic devices.
Catalysis:
Catalyst Layers: Deposition of catalytic materials on substrates for use in chemical reactions, fuel cells, and environmental applications.
Surface Engineering:
Protective Coatings: Deposits wear-resistant, corrosion-resistant, and thermal barrier coatings on various surfaces.
Functional Coatings: Imparts specific properties like hydrophobicity, antimicrobial activity, or electrical conductivity to surfaces.
Nanotechnology:
Nanostructured Films: Creates films with nanoscale features for use in sensors, MEMS (Micro-Electro-Mechanical Systems), and nanodevices.
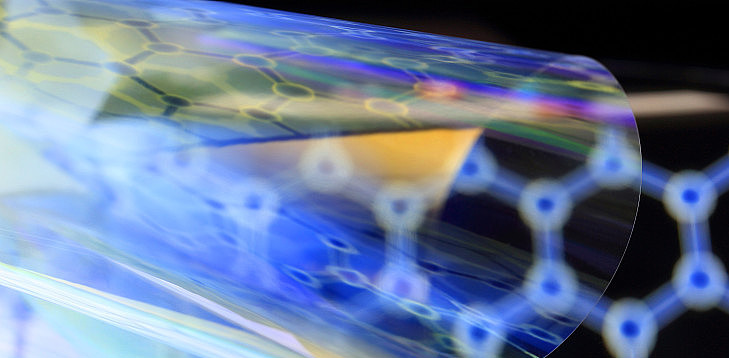
Advantages of AACVD
Broad Material Compatibility:
Capable of depositing a wide range of materials, including metals, ceramics, and composites.
High Uniformity:
Provides uniform coatings even on complex-shaped substrates.
Cost-Effective:
Uses liquid precursors that are often less expensive and easier to manage than gaseous ones.
Flexible Process:
Parameters can be easily adjusted to produce films with desired properties.
Limitations of AACVD
Complexity:
The process requires careful control of multiple parameters, making it more complex than some other deposition techniques.
Potential for Residues:
Depending on the precursor and solvent, residues or unwanted by-products may be left on the substrate, requiring additional cleaning steps.
Conclusion
The Aerosol-Assisted Chemical Vapor Deposition (AACVD) system is a powerful and versatile tool for the deposition of thin films and coatings across various industries.
Its ability to precisely control film properties, along with its scalability and cost-effectiveness, makes it an attractive choice for both research and industrial applications.
Whether in electronics, energy, or materials science, AACVD continues to play a critical role in advancing technology through innovative material deposition techniques.