Table of Contents
Introduction
Porous materials play a crucial role in various industries, including energy storage, catalysis, filtration, and biomedical applications. The sintering process is a key step in their fabrication, influencing porosity, mechanical strength, and functionality.
From laboratory-scale research to large-scale industrial production, selecting the right sintering method is essential for optimizing material performance.
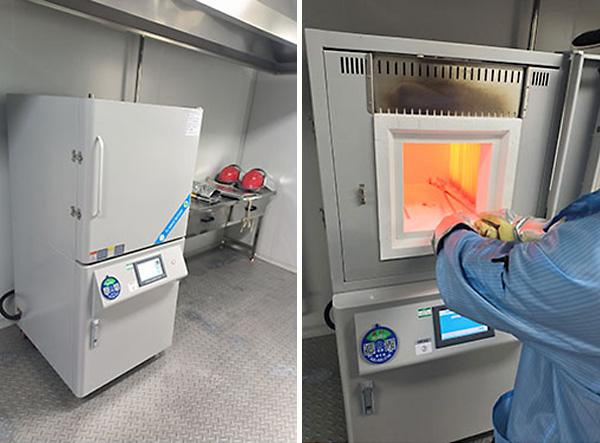
What is Sintering?
Sintering is a heat treatment process where powdered materials are compacted and heated below their melting point to create a solid, interconnected structure.
In the case of porous materials, careful control of temperature and atmosphere is required to maintain the desired porosity while enhancing mechanical stability.
Key Sintering Techniques for Porous Materials
1. Conventional Sintering
- Process: Powder compaction followed by heating in a furnace.
- Advantages: Simple and cost-effective for batch processing.
- Challenges: Limited control over pore size and distribution.
- Applications: Ceramic membranes, filtration components, and catalyst supports.
2. Spark Plasma Sintering (SPS)
- Process: Rapid heating with pulsed electric current.
- Advantages: Faster processing times, lower sintering temperatures, and improved material properties.
- Challenges: Limited scalability for large industrial applications.
- Applications: Advanced porous ceramics, battery electrodes, and high-performance filters.
3. Hot Pressing and Hot Isostatic Pressing (HIP)
- Process: Uses high pressure and temperature to densify materials.
- Advantages: Enhanced mechanical properties and precise pore control.
- Challenges: Expensive equipment and complex operation.
- Applications: High-strength porous metals and biomedical implants.
4. Microwave Sintering
- Process: Uses microwave energy to heat materials internally.
- Advantages: Faster heating rates and energy efficiency.
- Challenges: Requires specific material compositions for uniform heating.
- Applications: Porous ceramics and nanostructured materials.
5. Vacuum and Controlled Atmosphere Sintering
- Process: Sintering under reduced pressure or controlled gas environments.
- Advantages: Prevents oxidation and maintains purity in high-performance materials.
- Challenges: Requires specialized furnace systems.
- Applications: Metal-organic frameworks (MOFs), gas separation membranes, and fuel cell components.
Laboratory vs. Industrial Sintering
Laboratory-scale sintering focuses on research and material development, while industrial-scale sintering emphasizes efficiency, consistency, and scalability. Key considerations include:
- Temperature Precision: Lab furnaces offer better control for small-scale experiments.
- Atmosphere Control: Essential for preventing contamination in high-purity materials.
- Energy Efficiency: Industrial processes prioritize cost-effective energy usage.
- Scalability: Continuous sintering furnaces enable large-scale production.
Choosing the Right Furnace for Sintering Porous Materials
The selection of a sintering furnace depends on material properties, production scale, and application requirements. Common options include:
- Muffle Furnaces: Ideal for small-scale ceramic sintering and research.
- Tube Furnaces: Suitable for atmosphere-controlled sintering of advanced materials.
- Vacuum Furnaces: Essential for high-purity porous metals and MOFs.
- Continuous Sintering Furnaces: Designed for large-scale industrial applications.
Conclusion
The sintering process is a critical step in the development of porous materials, affecting their performance across multiple industries. Whether for laboratory research or large-scale industrial production, selecting the appropriate sintering technique and furnace type is essential for achieving optimal results.
Companies specializing in high-temperature sintering solutions can provide tailored furnace systems to meet the specific needs of porous material applications.
ZYLAB offers high-quality laboratory furnaces designed for precision and efficiency. Contact us today to find the best sintering furnace for your application.