Table of Contents
Introduction
Plasma-Enhanced Chemical Vapor Deposition (PECVD) furnaces are essential for thin-film deposition in industries such as semiconductors, optics, photovoltaics, and MEMS.
Choosing the right PECVD furnace is crucial to achieving high-quality film coatings with precise control over deposition parameters.
This guide will walk you through the key factors to consider when selecting a PECVD furnace that meets your research or production needs.
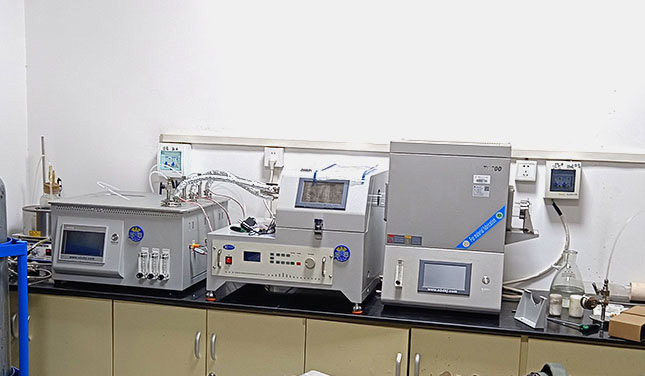
Substrate Compatibility
The first step in choosing a PECVD furnace is determining the type and size of the substrates you will be processing. Consider the following:
Material: Ensure the furnace can handle your substrate material, whether it’s silicon, glass, polymers, or metal.
Size and Shape: Choose a furnace with the appropriate chamber dimensions to accommodate wafers, panels, or custom-shaped substrates.
Temperature Sensitivity: Some materials require low-temperature processing to avoid degradation.
Deposition Materials and Process Requirements
Different PECVD systems are designed for specific material deposition. Make sure the furnace supports the thin films you need, such as:
- Silicon-based films: SiO2, Si3N4, amorphous silicon
- Carbon-based films: Diamond-like carbon (DLC), graphene
- Metal oxides: TiO2, Al2O3, ZnO
- Specialized coatings: Hydrophobic layers, barrier coatings
Additionally, consider:
- Deposition rate: Ensure the system provides the required film thickness and uniformity.
- Gas delivery system: A high-precision gas flow system is necessary for accurate film composition.
- Plasma power source: Choose between RF or microwave plasma depending on your process needs.
Temperature Control and Uniformity
PECVD furnaces must provide precise temperature control to ensure consistent deposition. Look for:
- Uniform heating: A well-designed furnace ensures uniform film properties across the substrate.
- Low-temperature operation: Some applications require deposition at temperatures as low as 200°C to prevent substrate damage.
- Thermal stability: The furnace should maintain stable conditions to avoid film defects.
Vacuum and Gas Handling System
A high-performance vacuum system is essential for maintaining process purity and film quality. Key aspects include:
- Vacuum level: A well-controlled vacuum prevents contamination and ensures proper plasma formation.
- Gas flow control: A precise mass flow controller (MFC) system regulates precursor gas composition for optimal deposition.
- Pump system: Dry pumps are preferred for minimizing contamination in high-purity applications.
Automation and Control System
Modern PECVD furnaces come with advanced automation and control features that improve reproducibility and ease of operation:
- Touchscreen interface: Allows easy adjustment of deposition parameters.
- Programmable recipes: Enables repeatable processes with stored parameters.
- Real-time monitoring: Ensures stability and allows process optimization.
- Data logging: Tracks deposition history for quality control.
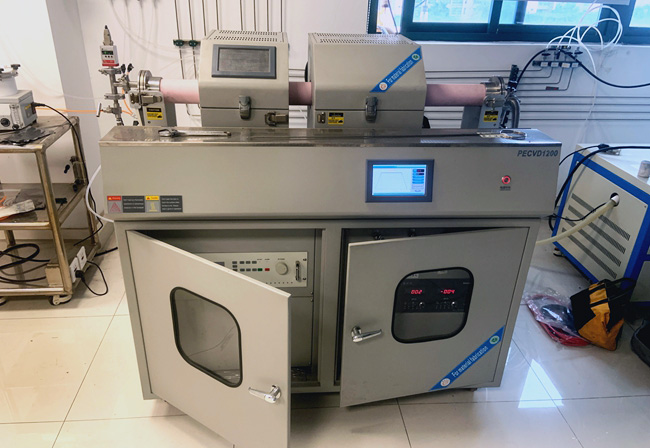
Scalability and Production Capacity
Whether you need a PECVD furnace for research or industrial production, scalability is a crucial factor:
- Batch vs. inline processing: Choose batch systems for R&D or inline systems for mass production.
- Chamber configuration: Dual-chamber designs improve throughput for high-volume applications.
- Customizability: Ensure the system can be upgraded with additional features as your needs evolve.
Reliability and Maintenance
Selecting a PECVD furnace with a reliable design minimizes downtime and operational costs. Consider:
- Durable chamber materials: Quartz, stainless steel, or aluminum chambers ensure longevity.
- Easy maintenance access: Systems with quick-access doors simplify cleaning and part replacement.Service support:
- Service support: Ensure the manufacturer provides technical assistance, spare parts, and software updates.
ZYLAB PECVD Furnace: Your Ideal Choice
ZYLAB offers cutting-edge PECVD furnaces designed for high-precision thin-film deposition. Our PECVD systems feature:
- Advanced plasma technology for uniform and high-quality coatings.
- Custom gas delivery systems for precise material deposition.
- Optimized temperature control for low-temperature processing.
- User-friendly automation for efficient operation and process monitoring.
- Scalable solutions suitable for both R&D and industrial production.
Whether you need a PECVD furnace for semiconductor research, MEMS fabrication, or optical coatings, ZYLAB provides reliable and customizable solutions to meet your specific requirements.
Conclusion
Choosing the right PECVD furnace requires careful consideration of substrate compatibility, deposition materials, temperature control, vacuum systems, automation, scalability, and maintenance.
By selecting a high-quality PECVD system like those offered by ZYLAB, you can achieve superior thin-film deposition with enhanced precision and efficiency.
Contact us today to find the best PECVD solution for your needs!