Table of Contents
Cylindrical cell are a form of battery typically characterized by a cylindrical-shaped casing. The primary purpose of this battery design is to provide high energy density and long cycle life. Cylindrical cell find widespread use in various applications, including portable electronic devices, power tools, electric vehicles, and energy storage systems.
One of the most common types of cylindrical cell is the lithium-ion battery, which has gained extensive use in modern electronic devices. Lithium-ion cylindrical batteries offer high energy density, lightweight design, and relatively long lifespan, making them an ideal choice for applications such as mobile devices and electric vehicles.
In the design of cylindrical cell, the positive and negative electrodes are usually located at both ends of the battery, while the electrolyte is filled inside the casing to ensure ionic conduction between the electrodes. The casing of cylindrical cell is typically made of metal or plastic, providing a certain level of sealing to prevent electrolyte leakage and ensure the safety performance of the battery.
It is worth noting that there are various types of cylindrical cell, including lithium-ion batteries, nickel-metal hydride batteries, nickel-cadmium batteries, etc. These batteries differ in chemical composition and performance, making them suitable for different application scenarios.
Applications and Industries of Cylindrical Cell
Consumer Electronics: cylindrical cell are widely used in mobile devices such as smartphones, tablets, and portable audio devices. Lithium-ion cylindrical cell are particularly common in these devices due to their high energy density and lightweight characteristics.
Power Tools: Power tools, such as electric drills, hammers, and saws, often use cylindrical cell as a power source. These batteries can provide sufficient energy while keeping the tools relatively lightweight and portable.
Electric Vehicles: Electric vehicles, including electric cars and electric bicycles, use cylindrical cell to provide ample electrical energy, extend driving range, and enhance overall performance.
Energy Storage Systems: Cylindrical cell play a crucial role in energy storage systems, such as solar and wind energy storage systems, for balancing grid loads and storing reserve power.
Medical Devices: Some medical devices, such as portable medical equipment and electric wheelchairs, also adopt cylindrical batteries to provide reliable power sources.
Military and Defense: Cylindrical cell are widely utilized in military and defense applications, including submarines, missile systems, and communication devices.
Aerospace: Certain aerospace applications, including satellites and spacecraft, also utilize cylindrical cell to provide power support.
Cylindrical Cell Preparation Process
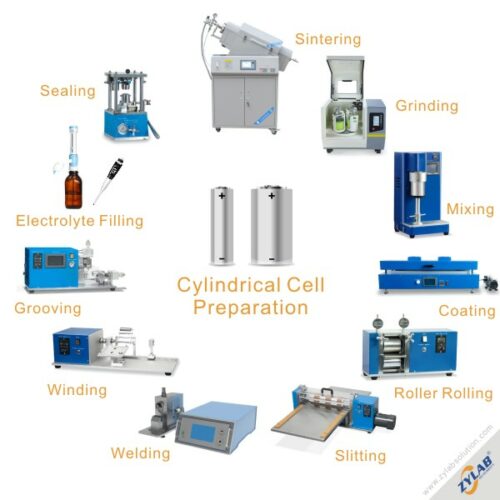
Material Preparation:
Collect positive electrode materials (such as oxides), negative electrode materials (such as graphite), electrolyte (usually liquid or colloidal, containing lithium salt), separator materials (polymer), and current collector materials (usually aluminum foil and copper foil).
Positive and Negative Electrode Material Preparation:
Positive Electrode Preparation:
Positive Electrode Material Selection: Choose appropriate positive electrode active materials, usually lithium compounds, such as lithium cobalt oxide (LiCoO2), lithium nickel manganese cobalt oxide (NMC), lithium iron phosphate (LFP), etc., based on battery performance and application requirements.
Positive Electrode Material Preparation: Positive electrode materials usually exist in powder form, and they are mixed with a conductive agent (usually carbon black) and a binder to form a slurry.
Coating: Coat the positive electrode slurry onto a conductive current collector (usually aluminum foil) to form a positive electrode sheet. The coating process may need to be carried out under specific humidity and temperature conditions to ensure a uniform coating.
Baking: Bake the coated positive electrode sheet to remove solvents and cure the binder, forming a stable positive electrode.
Cutting: Cut the positive electrode sheet into appropriate shapes and sizes to meet the requirements of battery design.
Negative Electrode Preparation:
Negative Electrode Material Selection: Choose appropriate negative electrode active materials, usually carbon materials (such as graphite) or silicon, based on battery performance and application requirements.
Negative Electrode Material Preparation: Negative electrode materials exist in powder form, and they are mixed with a conductive agent and a binder to form a slurry.
Coating: Coat the negative electrode slurry onto a conductive current collector (usually copper foil) to form a negative electrode sheet. The coating process may need to be carried out under specific humidity and temperature conditions to ensure a uniform coating.
Baking: Bake the coated negative electrode sheet to remove solvents and cure the binder, forming a stable negative electrode.
Cutting: Cut the negative electrode sheet into appropriate shapes and sizes to meet the requirements of battery design.
Separator Preparation:
Prepare polymer separators, ensuring they have an appropriate porous structure to facilitate lithium ion conduction while preventing direct contact between the positive and negative electrodes.
Electrolyte Injection:
Inject electrolyte between the positive and negative electrode sheets to form the electrolyte layer between the positive and negative electrodes of the battery.
Battery Assembly:
Layer positive and negative electrode sheets and separator layers together. Typically, this step needs to be completed in a dust-free room or a similar clean environment.
Encapsulation:
Seal the battery casing to prevent electrolyte leakage and ensure the safety of the battery. The casing is usually made of metal or plastic.
Charging and Testing:
Initiate the first charge of the battery and then conduct a series of tests, including capacity testing, charge/discharge efficiency testing, cycle life testing, etc., to ensure that the battery meets specification requirements.
ZYLAB recommends experimental equipment for cylindrical cell preparation:
The Role of High-Temperature Furnace in Cylindrical Cell Development
Sintering and Heat Treatment of Electrode Materials: High-temperature furnaces can be used for the sintering and heat treatment of electrode materials, promoting stronger particle bonding of electrode materials, improving electrode conductivity, and stability. This helps to enhance the energy density and cycle life of the battery.
Crystal Structure Modulation: The use of high-temperature furnaces can introduce changes in the crystal structure of electrode materials. Through heat treatment, the crystal lattice structure of electrode materials can be optimized, improving their conductivity and stability.
Separator Heat Treatment: Separators in cylindrical cell are used to separate the positive and negative electrodes, ensuring the conduction of lithium ions and preventing short circuits. Heat treatment with high-temperature furnaces can improve the thermal stability and mechanical performance of separators, thereby enhancing battery safety.
Heat Treatment in Battery Assembly: During the battery assembly process, high-temperature furnaces can be used to heat treat the entire battery to ensure the uniform distribution and solidification of internal components. This helps improve electrolyte permeability, ensuring battery consistency and performance.
Material Synthesis: In the development of cylindrical battery materials, high-temperature furnaces can also be used in the material synthesis process, such as synthesizing positive and negative electrode active materials through solid-state reactions.
Heat Treatment After Electrolyte Injection: After electrolyte injection, the use of high-temperature furnaces can facilitate electrolyte penetration and distribution, improving battery performance and cycle life.
Study on Battery Performance Impact: The use of high-temperature furnaces can be employed to study battery performance under high-temperature conditions, testing the stability and lifespan of battery materials, providing data support for improving battery design.
The application of high-temperature furnaces in the development of cylindrical cell helps optimize materials and processes, enhancing battery performance, safety, and stability.
Below are several high-temperature furnaces recommended by ZYLAB for your reference:
Feel free to contact our technical staff if you have any questions.