Table of Contents
Coin cell typically refer to small button cells with a shape resembling a coin. They are designed in a disc-like or coin-like form. These batteries usually utilize lithium, silver oxide, or alkaline battery technologies.
Coin batteries are primarily used in small electronic devices and some specific applications, featuring a compact design and adaptability.
Basic Steps for Coin Cell Preparation
Materials Preparation
Positive and negative electrode materials: Choose appropriate positive and negative electrode materials, typically metal oxides, sulfides, etc.
Electrolyte: Choose a suitable electrolyte, usually a liquid electrolyte, for ion conduction between the positive and negative electrodes.
Electrode Preparation
Prepare positive and negative electrode slurries: Mix positive and negative electrode materials with conductive additives, binders, etc., to form electrode slurries.
Coat electrodes: Coat the electrode slurries onto a conductive substrate, typically choosing a flexible substrate such as medical tape.
Drying
Dry the coated electrodes to remove solvents and moisture, making the electrode sheets more robust.
Sintering
Place the electrode sheets in a sintering furnace and subject them to high temperatures, allowing the electrode material particles to bind more tightly, enhancing conductivity and mechanical strength.
Assembly
Stack positive and negative electrodes with electrolyte in between to form the battery structure.
Add a separator: Place an ion-conductive separator between the positive and negative electrodes to prevent short circuits.
Encapsulation
Place the assembled battery in an encapsulation container, sealing it to prevent electrolyte leakage.
The encapsulation container is typically made of metal or plastic.
Testing and Analysis
Perform performance tests on the prepared button cell, including capacity, charge-discharge performance, etc.
Conduct structural analysis, such as using scanning electron microscopy (SEM) to understand the microstructure of the electrode materials.
Charge and Discharge Cycle Testing
Conduct multiple charge and discharge cycle tests to evaluate the battery’s cycle life and stability.
Optimization Experiment
Based on test results and analysis, conduct necessary optimization experiments to improve battery performance and stability.
This is a general process for the preparation of coin cell batteries, and specific experiments may vary depending on different materials and special requirements of the experiment.
In button cell batteries, electrode material sintering is a crucial preparation step, and the sintering furnace is the equipment used to complete this step.
Role of the Sintering Furnace in Coin Cell Preparation
Sintering electrode particles: In button batteries, electrode materials are typically in the form of particles, such as metal oxides or sulfides. Through the sintering furnace, these particles can be heated to high temperatures, causing them to form stronger bonds between particles, improving the mechanical strength and conductivity of the electrode material.
Formation of a uniform structure: The sintering process helps form a uniform electrode structure, ensuring good electronic and ionic conduction channels inside the electrode. This is crucial for enhancing battery performance and cycle life.
Removal of organic compounds: In the preparation of electrode materials, there may be some organic compounds, such as polymer binders. The high-temperature environment of the sintering furnace helps thermally decompose or volatilize these organic compounds, making the electrode material purer.
Activation of electrode materials: In some cases, electrode materials may need certain heat treatment to activate their electrochemical properties and improve their response to ions and electrons.
Overall, the sintering furnace plays a crucial role in coin cell preparation experiments. By controlling temperature and processing time, the structure and performance of electrode materials can be optimized, thereby improving the performance and reliability of button cell batteries.
How to Choose the Right Sintering Furnace
Temperature Range: Understand the sintering temperature requirements of the electrode materials used and choose a sintering furnace with a sufficiently high temperature range. Ensure that the maximum temperature of the sintering furnace can meet the sintering requirements of the electrode material.
Control Accuracy: Precise temperature control is crucial during the battery preparation process. Choose a sintering furnace with a high-precision temperature control system to maintain stable temperatures throughout the sintering process.
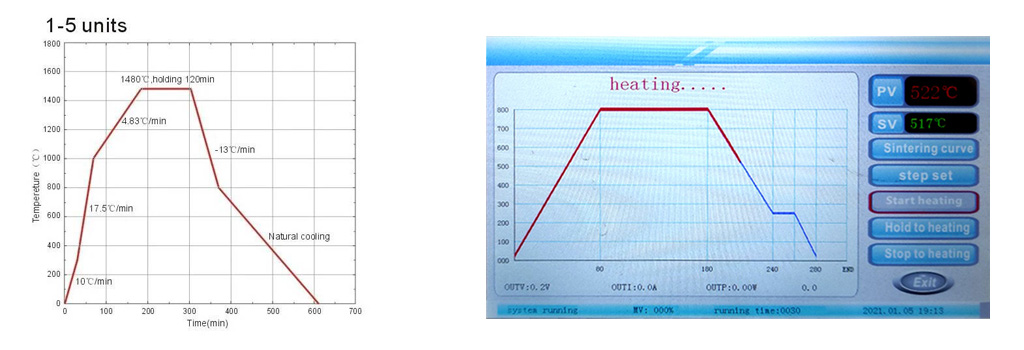
Heating Rate: Understand whether the electrode materials are sensitive to heating rate. Some materials may require a slower heating rate to avoid uneven sintering. Choosing a sintering furnace with an adjustable heating rate may be beneficial.
Furnace Atmosphere: For some special electrode materials, sintering may need to be carried out in an inert atmosphere to prevent oxidation or other reactions. Choose a sintering furnace that can provide an inert atmosphere, such as a nitrogen or argon atmosphere.
Furnace Material: When selecting furnace materials, consider compatibility with the electrode materials. Ensure that the chosen furnace material does not contaminate or react with the electrode material.
Furnace Size: Ensure that the furnace size of the sintering furnace is suitable for batch preparation of electrode materials, improving experimental efficiency.
Safety and Usability: Choose a sintering furnace with good safety and usability features, including a safe control system and an easy-to-operate interface.
Preheating and Cooling Systems: Some sintering furnaces have rapid preheating and cooling systems, which can be helpful for improving experimental efficiency and shortening experiment time.
Programmability: Sintering furnaces with programmable control systems can adapt more flexibly to different sintering curves and experimental requirements.
The preparation experiment for button cell batteries is crucial, and by optimizing the preparation process, battery performance, cycle life, and safety can be improved, ensuring their suitability for various application scenarios. Therefore, in-depth research and continuous optimization of button cell battery preparation experiments are key factors driving the development of microelectronic devices, portable devices, and embedded systems.
Here are the sintering furnaces recommended by ZYLAB for your reference.
Feel free to contact our technical staff if you have any questions.